Sergio76
Mechanical
- Apr 11, 2012
- 28
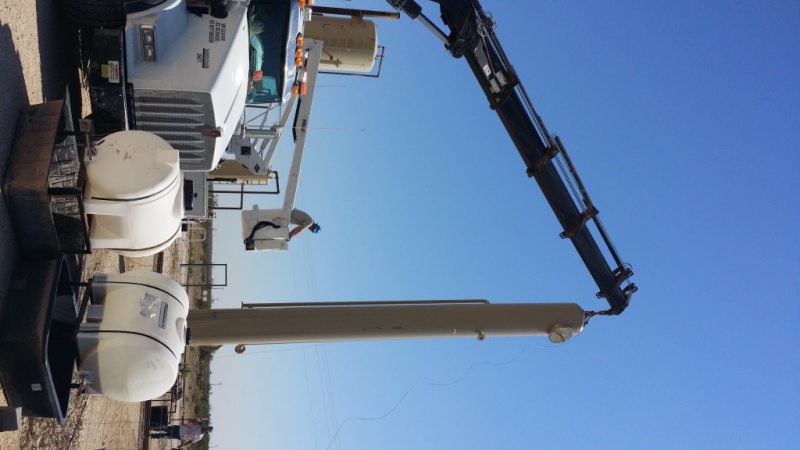
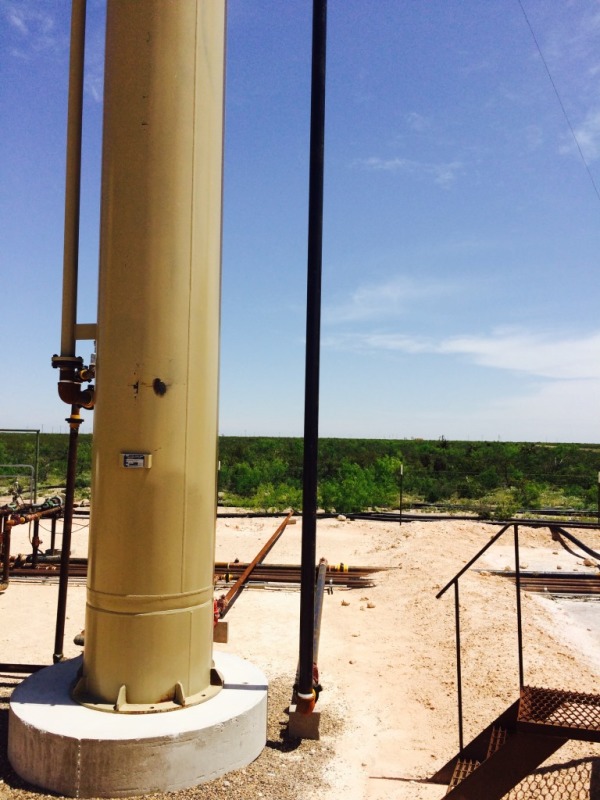

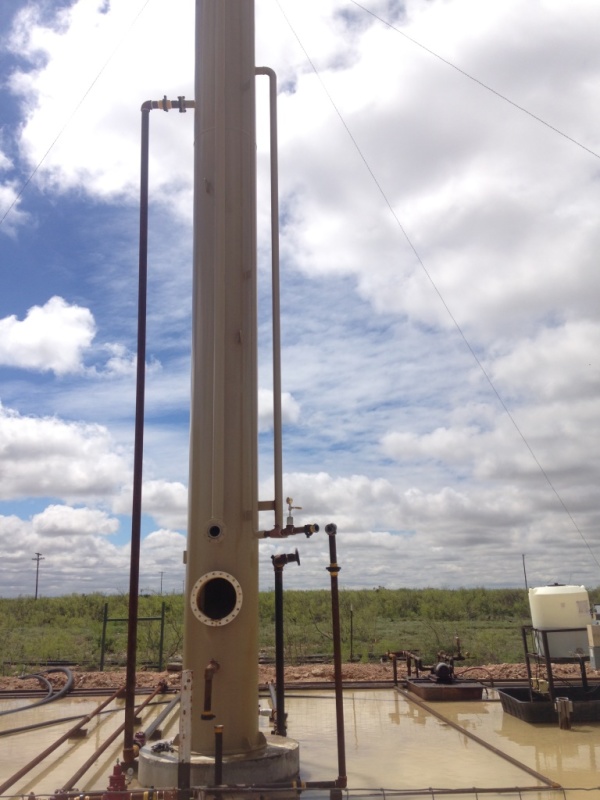
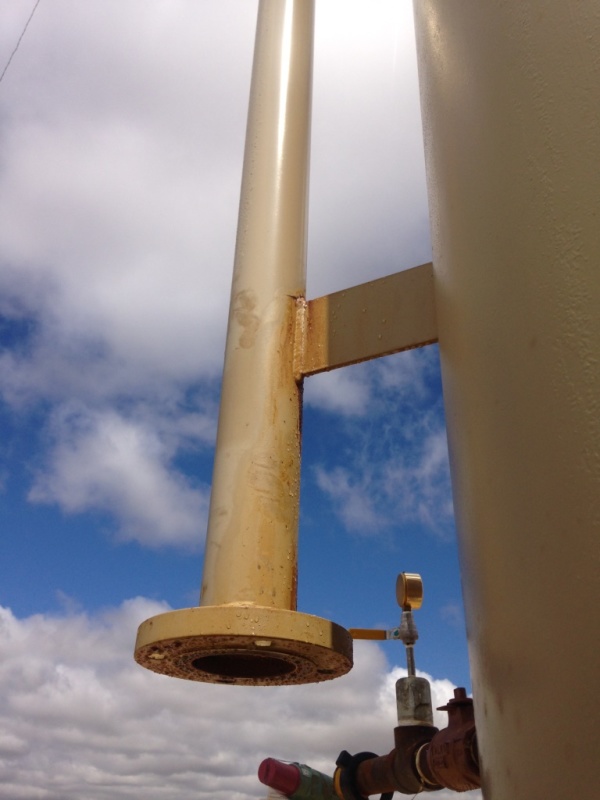
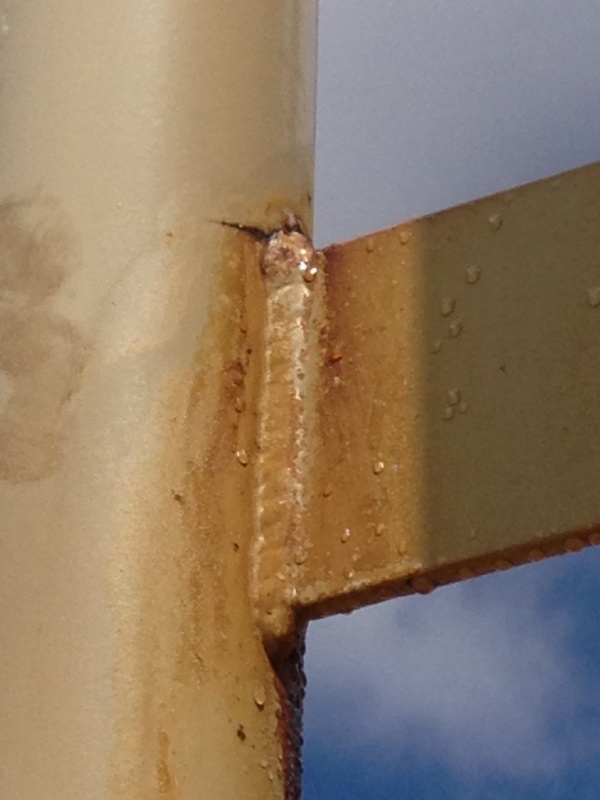
Hello all, I have some equipment as shown in the pictures that have a pipe failure at the support attached.
This is a Vertical Recovery Tower 30" OD X 30' S/S operating at 50 PSI @ 100 F. According to the field foreman, the vessel started leaking 30 min after operation start.
my concerns about this failure were:
1.Transportation and erection procedure, but apparently all pipes are free from any erection load.
2.Material of origin, I checked the MTRs, and the material is according to SA-106,B Smls pipe.
3.Looking at the pictures, there appears to be pipe hanging off of the vessel connections and the pipe is supported by bricks, not concrete foundations. These foundations are probably not offering any support, vertically nor laterally. The pipe seems to be just resting on the bricks. I think it could be a vibration problem, because we cannot see where the pipes go. I suggest the customer should have poured concrete bases for the pipe supports, then secure the pipe with brackets and u-bolts. I think the customer’s pipe is not adequately supported and there must be some type of oscillating load. The failure look like fatigue, normally seen at a compressor station.
I have not be exposed to much to this kind of failures, I would appreciate if someone could guide me to figure out what could be the possible cause of this pipe fracture.
thanks a lot.