Hey everyone,
I have a project that I am working where I am designing a plate mounted/fixed to a heavy duty rotary actuator; the actuator is fixed. A 100kg blocked is clamped to it and upon it a 300kg weight is clamped. The whole plate length is 1.6m long with the actuator sitting 0.4m from one end.
My objective as given by my supervisor is to design a plate which when loaded has max deflection of 5 microns.
I modeled it as a cantilever beam and did some hand calculations and the thickness came out to be 350mm which was an immediate no. The plate thickness has to be within 100mm
How do I model this in SolidWorks CAE, what boundary conditions do I give it? I was suggested by my senior engineer that when two parts are clamped tight, it adds some stiffness. How do I factor all that in? I have attached a picture for reference.
TL;DR - How to model the Plate in the below picture accurately in SolidWorks CAE in the way it is mounted and clamped. Please suggest.
Material of Plate is A36 HRS
I really appreciate you all for taking time to read this length post.
I have a project that I am working where I am designing a plate mounted/fixed to a heavy duty rotary actuator; the actuator is fixed. A 100kg blocked is clamped to it and upon it a 300kg weight is clamped. The whole plate length is 1.6m long with the actuator sitting 0.4m from one end.
My objective as given by my supervisor is to design a plate which when loaded has max deflection of 5 microns.
I modeled it as a cantilever beam and did some hand calculations and the thickness came out to be 350mm which was an immediate no. The plate thickness has to be within 100mm
How do I model this in SolidWorks CAE, what boundary conditions do I give it? I was suggested by my senior engineer that when two parts are clamped tight, it adds some stiffness. How do I factor all that in? I have attached a picture for reference.
TL;DR - How to model the Plate in the below picture accurately in SolidWorks CAE in the way it is mounted and clamped. Please suggest.
Material of Plate is A36 HRS
I really appreciate you all for taking time to read this length post.
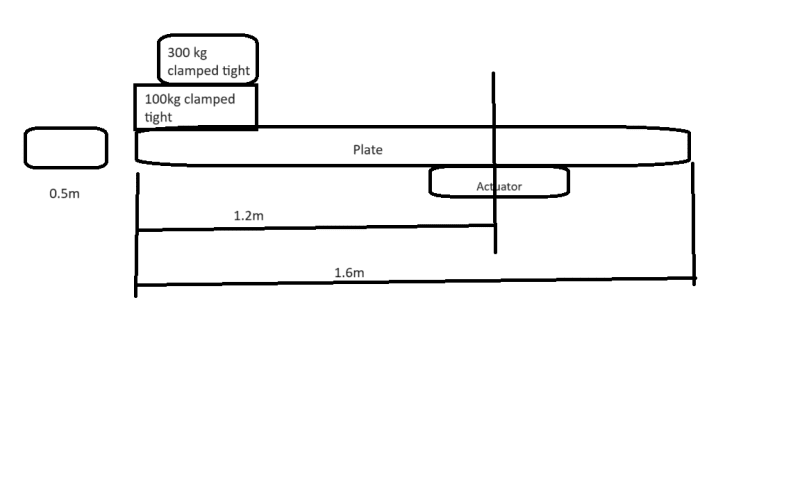