MattEdwards
Mechanical
In this example, axis C is a tertiary datum for several other features, locating them in the left-right direction. If axis C is not perfectly perpendicular to datums A & B, this seems to create an ambiguous datum. Each end of axis C could be at a slightly different left-right position. How would this be handled during inspection? Is the centre point of axis C used as the datum?
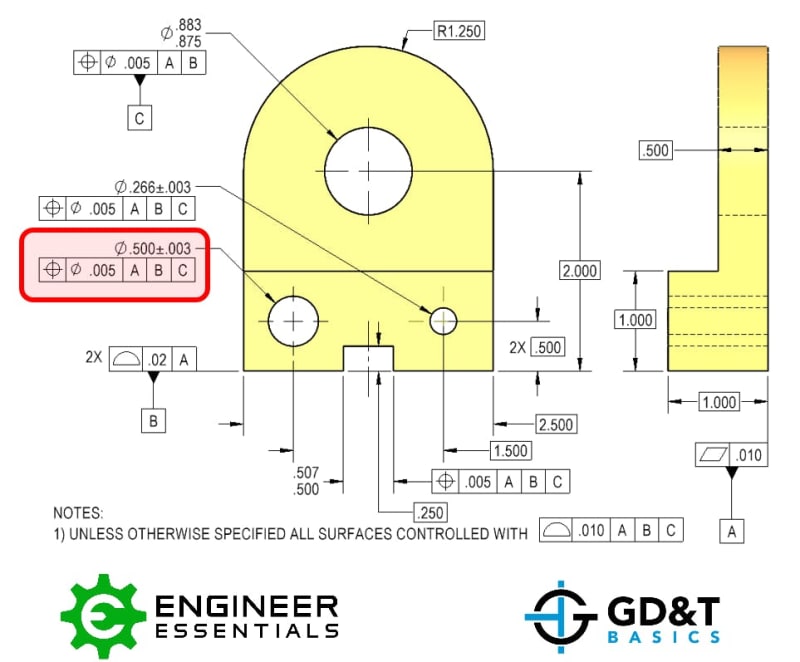