Billzilla
Aerospace
- Jun 14, 2017
- 9
I'm designing a V8 engine, mainly for the challenge, and I've been trying to decide on either a conventional billet crankshaft or a press-together one. I have no doubts that the plain billet crank would work just fine, but I don't want to discount the advantages of a press-together type as it makes the machining to get the rotation mass down a bit easier. I thought that with the very accurate tolerances available with good EDM gear, I could make the connecting surfaces have shapes that aren't the typical round profile that's locked together with a spot of weld, but, for example, have a round section that has two parallel sides on it. That would lock the various parts together quite accurately & firmly.
I was also wondering about the strength of such a PTG crank, as it wouldn't have the stress areas around the journals like a regular crank would.
So, any thoughts or suggestions please?
Note that I haven't calculated the counterweight masses & sizes, so the pictured cranks are just as an example.
I was also wondering about the strength of such a PTG crank, as it wouldn't have the stress areas around the journals like a regular crank would.
So, any thoughts or suggestions please?
Note that I haven't calculated the counterweight masses & sizes, so the pictured cranks are just as an example.
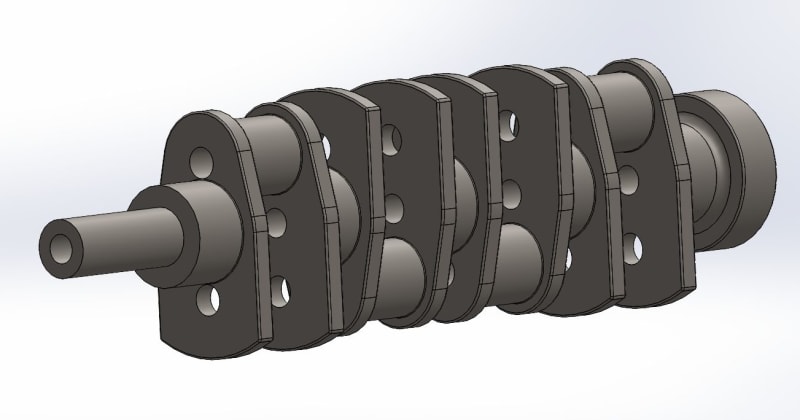
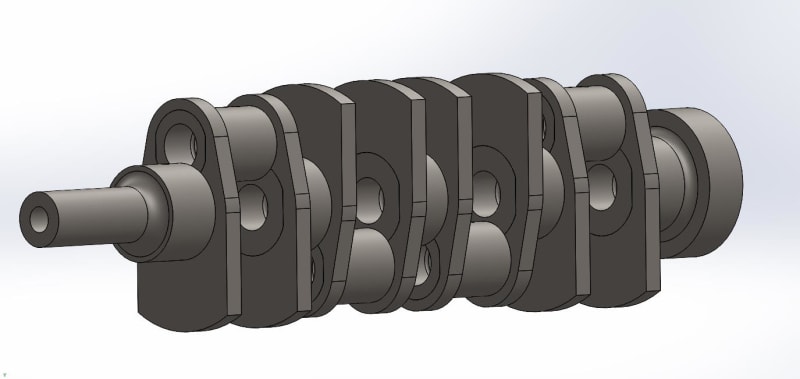