CADCAMTech
Mechanical
I am trying to calculate the amount of force that is applied to a fitting, when an internal pressure is applied to it. The red line shows the area where the pressure is applied, the blue dot is the shear screws, and the yellow arrow is the direction the fitting moves when the screw shears. The end goal is to calculate the number of shear screws I will need.
If you look at the attached images below you can see how I calculated the angled areas which I applied the 7000 psi pressure to. Then I calculated the force based on my known pressure and the known surface area with the pressure acting perpendicular to the surface, and finally I solved for the x direction of the force for each angled area.
The final value I ended up with (18871 lbf) was much larger than I was expecting and does not correlate with older data we have. Previous tests have shown that a pressure of approx. 3000 psi is needed to shear 3 screws, but this was all done by testing, no previous hand calculations exist for this product that I can find.
So I am wondering where I have went wrong:
If anyone is able to help point me in the right direction for what I am trying to do it would be appreciated, Thanks.
(to make things worse, I have no idea what the yield strength of the shears screws is. The drawing says it should be 304 SS at 35ksi min yield, but the PO I tracked down says the screws are 316 SS conforming to ASTM F880(CW) but no grade is listed and I have not been able to find out what that ASTM document specifies. I have hardness tested several of the screws and they seem to be around 96 HRB)
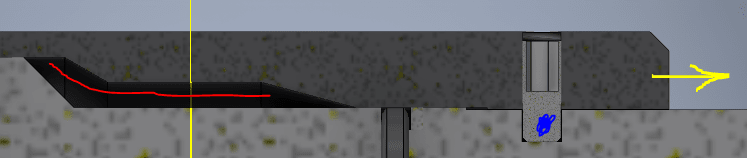
If you look at the attached images below you can see how I calculated the angled areas which I applied the 7000 psi pressure to. Then I calculated the force based on my known pressure and the known surface area with the pressure acting perpendicular to the surface, and finally I solved for the x direction of the force for each angled area.
The final value I ended up with (18871 lbf) was much larger than I was expecting and does not correlate with older data we have. Previous tests have shown that a pressure of approx. 3000 psi is needed to shear 3 screws, but this was all done by testing, no previous hand calculations exist for this product that I can find.
So I am wondering where I have went wrong:
1. When you look at F1 and F2 below, should I only be using the higher value instead of adding them together? To me both surfaces contribute to the force in the x-direction.
2. I assumed that the max distortion energy criterion applied to the shear screws where shear=0.577Sy is this correct?
If anyone is able to help point me in the right direction for what I am trying to do it would be appreciated, Thanks.
(to make things worse, I have no idea what the yield strength of the shears screws is. The drawing says it should be 304 SS at 35ksi min yield, but the PO I tracked down says the screws are 316 SS conforming to ASTM F880(CW) but no grade is listed and I have not been able to find out what that ASTM document specifies. I have hardness tested several of the screws and they seem to be around 96 HRB)
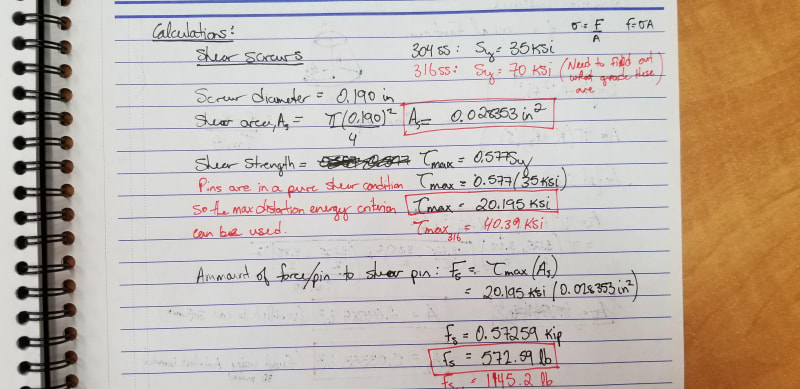
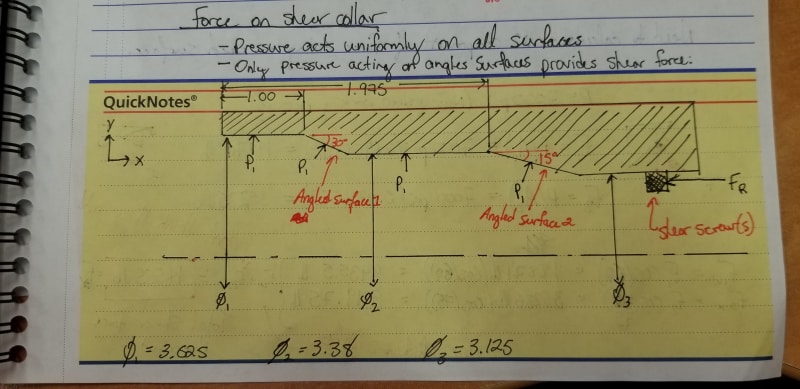
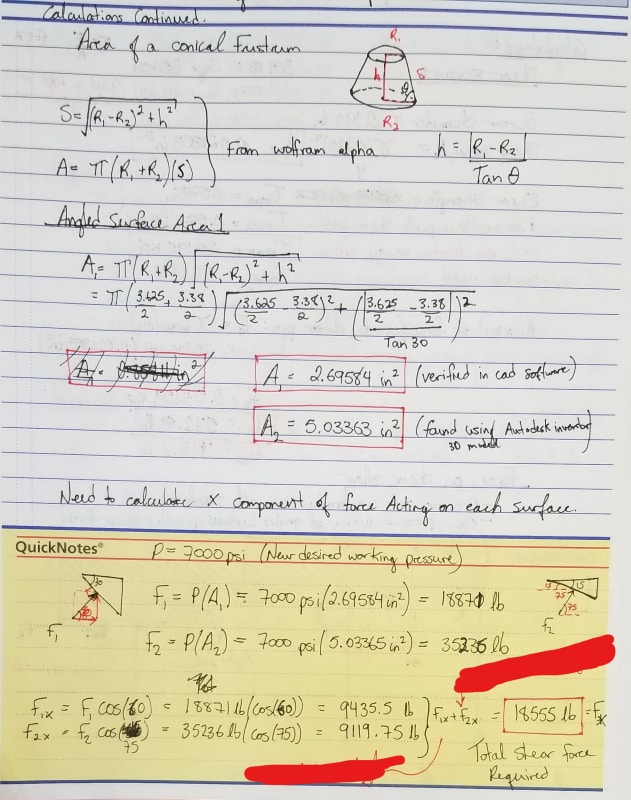