AMontembeault
Mechanical
I have a cylinder (actually a "pipe"), from which I establish datum "A" as the axis of the OD of the cylinder, datum B as an end of the cylinder, and datum C from a hole drilled into the side of the cylinder.
On the OD of the cylinder, I have to machine a grooved contour, one that presents itself as a projected rectangle or circle along its perimeter, and as a semi-circle (non-FOS) in any cross section. Below is a quick and dirty example of what I'm trying to describe, with the contour highlighted (numbers are just made up and do not necessarily reflect what we're really dealing with).
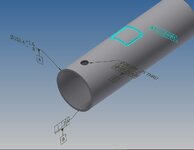
Initially, these contours were controlled by surface profile with respect to datums A|B|C. The problem is, we really want the depth of these contours set from the OD surface, because there is a considerable, unavoidable tolerance on the OD of the cylinder, and we're running into CMM issues when inspecting these contours with respect to datum axis A.
Is a directly toleranced dimension on depth unavoidable? if so, how would I go about controlling the other parameters of the contour? I'm not sure the overall perimeter meets the definition of a FOS (at least, not radially), and I know the groove cross section isn't a FOS, so my gut feels that using positional tolerance seems iffy. Im curious to know how others would approach this.
On the OD of the cylinder, I have to machine a grooved contour, one that presents itself as a projected rectangle or circle along its perimeter, and as a semi-circle (non-FOS) in any cross section. Below is a quick and dirty example of what I'm trying to describe, with the contour highlighted (numbers are just made up and do not necessarily reflect what we're really dealing with).
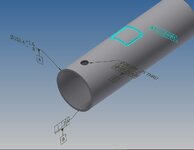
Initially, these contours were controlled by surface profile with respect to datums A|B|C. The problem is, we really want the depth of these contours set from the OD surface, because there is a considerable, unavoidable tolerance on the OD of the cylinder, and we're running into CMM issues when inspecting these contours with respect to datum axis A.
Is a directly toleranced dimension on depth unavoidable? if so, how would I go about controlling the other parameters of the contour? I'm not sure the overall perimeter meets the definition of a FOS (at least, not radially), and I know the groove cross section isn't a FOS, so my gut feels that using positional tolerance seems iffy. Im curious to know how others would approach this.