Hello everyone,
I'm overwhelmed by the amount of information regarding GD&T profile and I can't seem to find my answer here (or I got exhausted trying to understand all the information)
We have a small part with a sphere surface.
Based on ASME Y14.5-2018 is this dimensioning correct?
I'm currently modeling an assembly with parts at MMC to check for intersections and functionality. But when I looked at this drawing I got confused how to calculate the maximum material condition. (i.e. smallest sphere size)
Is it true when the sphere surface is at it's minimum size, the form has to be perfectly spherical, which is impossible to achieve?
Does the 0.05 profile refine the size tolerance? For me, it's confusing because if I go down in size, for e.g. at 12.92 I could no longer have a 0.05 profile tolerance.
Would it be reasonable to control the size, location and form with only the surface callout and basic dimensions?
Like |profile|0.05|A|B| and |SR13| and theoretical shpere center |14| are basic.
I'm overwhelmed by the amount of information regarding GD&T profile and I can't seem to find my answer here (or I got exhausted trying to understand all the information)
We have a small part with a sphere surface.
Based on ASME Y14.5-2018 is this dimensioning correct?
I'm currently modeling an assembly with parts at MMC to check for intersections and functionality. But when I looked at this drawing I got confused how to calculate the maximum material condition. (i.e. smallest sphere size)
Is it true when the sphere surface is at it's minimum size, the form has to be perfectly spherical, which is impossible to achieve?
Does the 0.05 profile refine the size tolerance? For me, it's confusing because if I go down in size, for e.g. at 12.92 I could no longer have a 0.05 profile tolerance.
Would it be reasonable to control the size, location and form with only the surface callout and basic dimensions?
Like |profile|0.05|A|B| and |SR13| and theoretical shpere center |14| are basic.
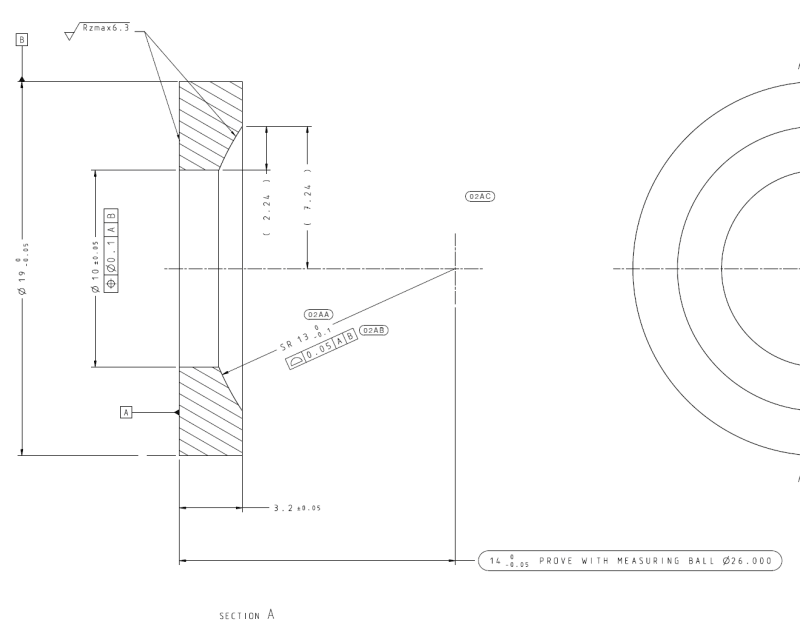