Hello everyone,
I have an issue about the interpretation on one of our component drawing.
It's a complex component, semifinished casting, which dimensions have to be checked.
On the drawing an overall profile tolerance is applied on every feature(2mm respect to A-B-C Datum). I attach a simple image to explain:
In order to be aligned with the supplier, which is the tolerance value to be considered on the 20 mm dimension (hole distance)?
I know that should have been better to choose a location tolerance for holes.
Can profile tolerance be used for location control?
If so, I think that the result should be 20 +/- 2 mm. Am I right?
Thanks to everyone who will help me.
Nicola
I have an issue about the interpretation on one of our component drawing.
It's a complex component, semifinished casting, which dimensions have to be checked.
On the drawing an overall profile tolerance is applied on every feature(2mm respect to A-B-C Datum). I attach a simple image to explain:
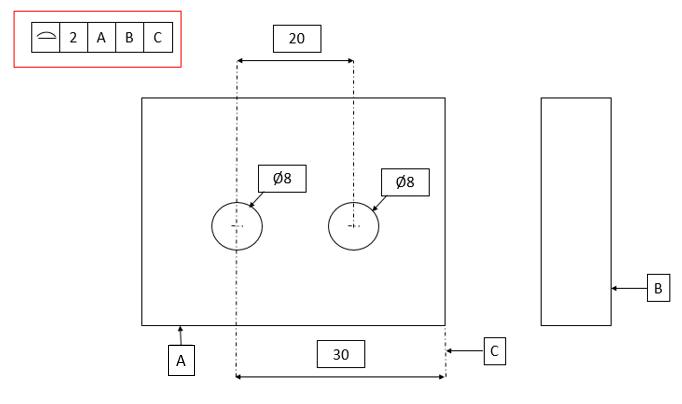
In order to be aligned with the supplier, which is the tolerance value to be considered on the 20 mm dimension (hole distance)?
I know that should have been better to choose a location tolerance for holes.
Can profile tolerance be used for location control?
If so, I think that the result should be 20 +/- 2 mm. Am I right?
Thanks to everyone who will help me.
Nicola