Pirate2719
Industrial
I have a weldment that we are working on bringing to market. Customers are asking for a more durable welded assembly for longevity. I am trying to achieve a 50-60 Rc Hardness throughout the part. I initially was suggested a 1045 material to machine to size, weld, and heat treat (stress relief of the assemblies prior to case hardening). The price of machining bar stock is driving up the cost tremendously going this route.
I have link showing the picture of the subject weldment sample I just received from my customer.
I have tested the hardness on it and results were Rc 55. Customer has no idea of material other than carbon steel. I have had a PMI done and have attached the snapshot I took from the analyzer.
I have measured its size and material seems to be of standard pipe size, but I have not ruled out tubing either. The larger section has a barely visible seam (seamless pipe or tube) and smaller seam has a visible weld seam. All ends are tapped to there respective pipe sizes of 2 NPT & 1-1/4 NPT
I have had a heat-treat facility tell me to stay away from Alloy Steels?? A machine shop is telling me to staying away from structural pipe?? I am confused at this point of what direction to take on material selection and was looking to some pro's to give some advice.
Thanks in advance.
Ben
I have link showing the picture of the subject weldment sample I just received from my customer.
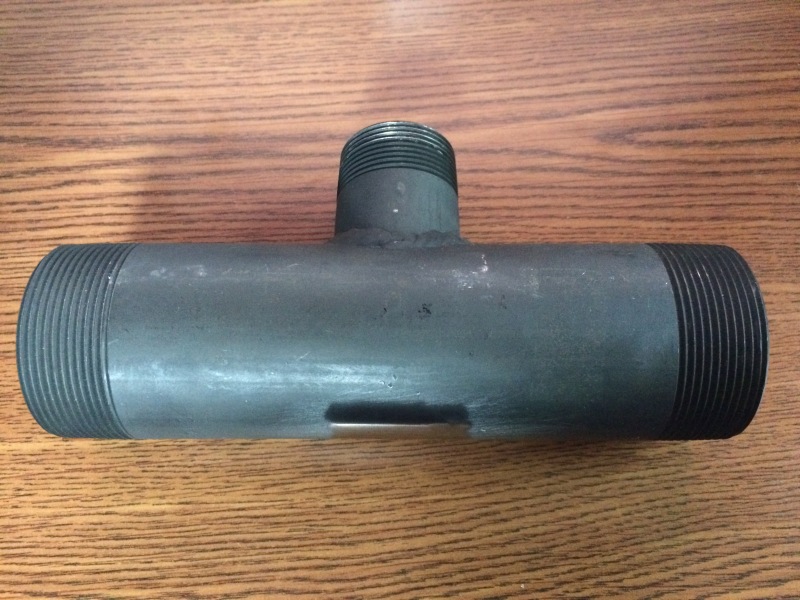
I have tested the hardness on it and results were Rc 55. Customer has no idea of material other than carbon steel. I have had a PMI done and have attached the snapshot I took from the analyzer.
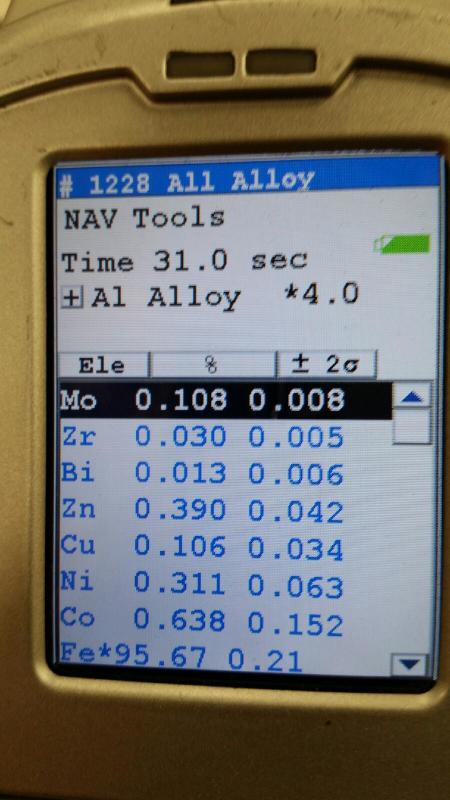
I have measured its size and material seems to be of standard pipe size, but I have not ruled out tubing either. The larger section has a barely visible seam (seamless pipe or tube) and smaller seam has a visible weld seam. All ends are tapped to there respective pipe sizes of 2 NPT & 1-1/4 NPT
I have had a heat-treat facility tell me to stay away from Alloy Steels?? A machine shop is telling me to staying away from structural pipe?? I am confused at this point of what direction to take on material selection and was looking to some pro's to give some advice.
Thanks in advance.
Ben