tmalik3156
Structural
- Jun 21, 2021
- 106
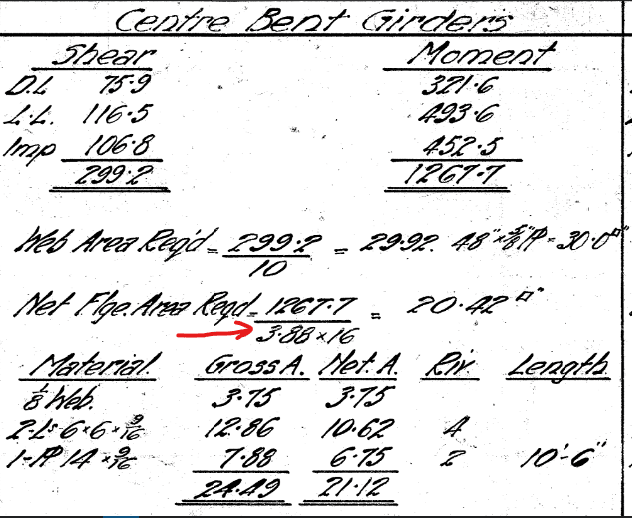
Hello all,
Attached is the calculation of proportioning a girder of an old bridge.
Can someone help me in understanding what this 3.88 is?
Let me explain in detail. In those days, the yield strength of structural steel was 29 ksi.
So, the allowable stress in shear was 0.35Fy = 10 ksi, and in bending 0.55Fy = 16 ksi.
As you can see, they calculated the shear load of 299.2 kip, and then divided by 10 ksi to get the required web area which is 48 inch by 5/8 inch. This is easy to understand.
But then to get the flange area, they are dividing the moment by 16 ksi, and also by 3.88 to get a flange area of 20.42 sq inch.
Then they use one-eighth of the web plus double angles plus a plate to get the required area.
I wonder what this 3.88 is! Can anyone figure out?