Liad
Chemical
- Feb 25, 2021
- 15
Hey all,
We are running a system with 3 positive gear pumps in parallel that installed at the outlet of a tank, like the picture below:
The left pump is the closest pump to the tank.
The outlet of the tank is 1.5", going up to suction of the pump is 3/4" for each pump and the discharge pipe is 1/2".
On each pipe coming out of the pump we installed an very accurate mass flow meter.
We are facing an issue when we are working in 2 or 3 pumps. when running a single pump the flow is stable.
When working with two pumps, the pump that closer to the tank having fluctuations in flow, while the pump that is further away has a very stable flow.
When we are working with 3 pumps, the pump that closest to the tank has fluctuations and the other 2 are very stable.
The flow is the same in one/two or three pumps.
I would be happy for your opinion on the subject, I assume that the reason is losses in head suction, but from calculations I have made there should be no problems.
Thanks in advance.
We are running a system with 3 positive gear pumps in parallel that installed at the outlet of a tank, like the picture below:
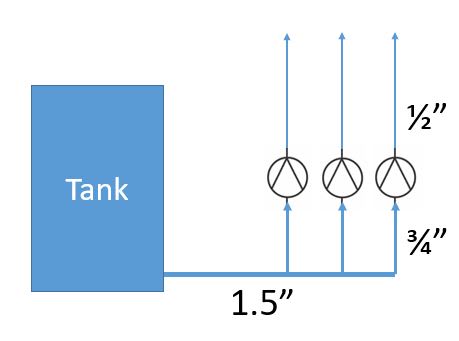
The left pump is the closest pump to the tank.
The outlet of the tank is 1.5", going up to suction of the pump is 3/4" for each pump and the discharge pipe is 1/2".
On each pipe coming out of the pump we installed an very accurate mass flow meter.
We are facing an issue when we are working in 2 or 3 pumps. when running a single pump the flow is stable.
When working with two pumps, the pump that closer to the tank having fluctuations in flow, while the pump that is further away has a very stable flow.
When we are working with 3 pumps, the pump that closest to the tank has fluctuations and the other 2 are very stable.
The flow is the same in one/two or three pumps.
I would be happy for your opinion on the subject, I assume that the reason is losses in head suction, but from calculations I have made there should be no problems.
Thanks in advance.