ndpaintballer
Mechanical
We are trying to control overall bow of an extruded vinyl profile. For a 200" lineal length piece, max of 2" bow is what supplier can control.
I've added a quick sketch to try and explain better.
Would a straightness callout on bottom of profile be the best way to call this out? This is assuming that the entire profile bends when that surface is bent and not just that bottom surface.
or would profile tolerance be better for this scenario?
Thanks!
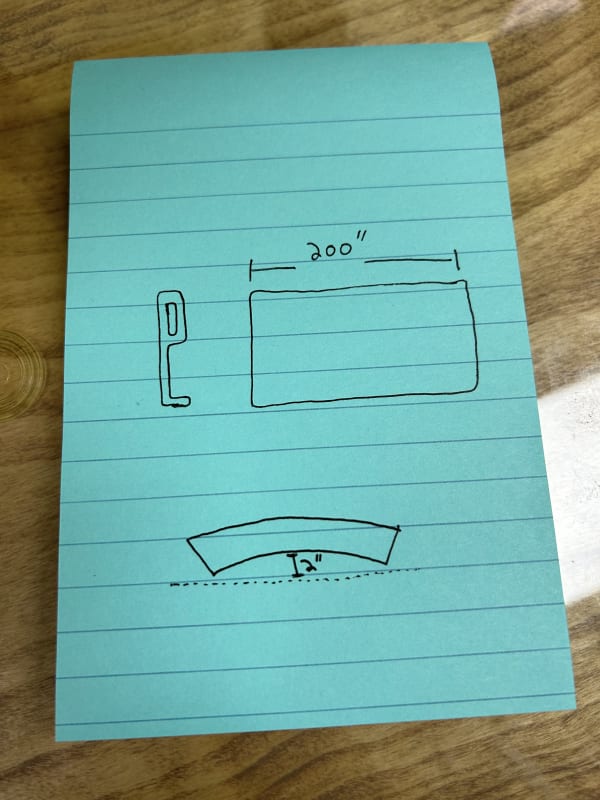
I've added a quick sketch to try and explain better.
Would a straightness callout on bottom of profile be the best way to call this out? This is assuming that the entire profile bends when that surface is bent and not just that bottom surface.
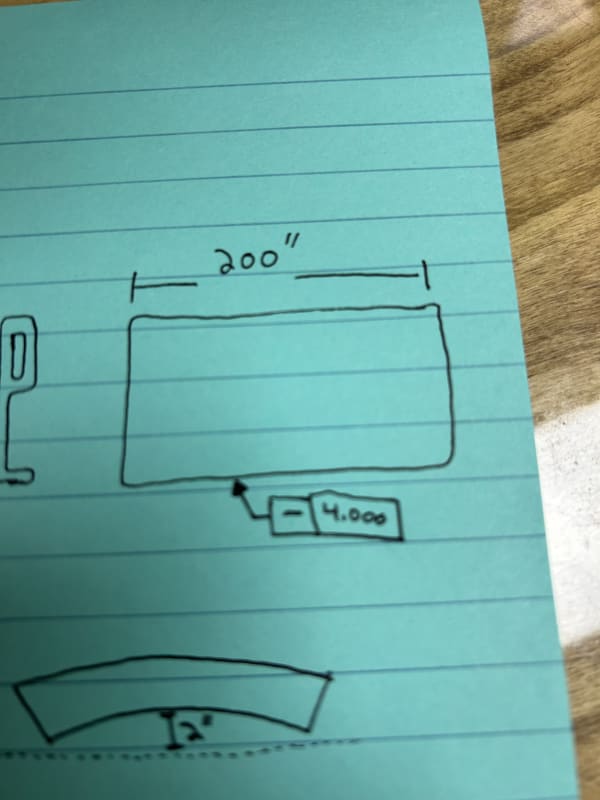
or would profile tolerance be better for this scenario?
Thanks!