human909
Structural
- Mar 19, 2018
- 2,070
Hi all. I though I'd throw this question out to the masses for a few ideas.
I need to seriously stiffen some members due to some vibrational issue. Cost of steel isn't really the issue it is more labour and looking for the easier and quickest solution to stiffen some existing beams. I'm mostly looking at three options and are after opinions but other suggestion are welcome.
I also want to know how effective bolting beams together can be and whether adequately rigid shear connection can be achieve to ensure that the beam acts compositely with the added member. I would presume slip critical bolting would be required and so make the whole process more difficult and possibly impractical.
Options I'm considering:
1: Welded T piece
2: Welded Wide flange (advantage being downwards facing welds)
3: Bolted member identical to existing (advantage being avoids site welds, but might be negated but number of bolts and slip critical requirements)
Overall I'm thinking option 2 is best but I'd like further input, particularly regarding option 3. Thanks.![[thumbsup] [thumbsup] [thumbsup]](/data/assets/smilies/thumbsup.gif)
I need to seriously stiffen some members due to some vibrational issue. Cost of steel isn't really the issue it is more labour and looking for the easier and quickest solution to stiffen some existing beams. I'm mostly looking at three options and are after opinions but other suggestion are welcome.
I also want to know how effective bolting beams together can be and whether adequately rigid shear connection can be achieve to ensure that the beam acts compositely with the added member. I would presume slip critical bolting would be required and so make the whole process more difficult and possibly impractical.
Options I'm considering:
1: Welded T piece
2: Welded Wide flange (advantage being downwards facing welds)
3: Bolted member identical to existing (advantage being avoids site welds, but might be negated but number of bolts and slip critical requirements)
Overall I'm thinking option 2 is best but I'd like further input, particularly regarding option 3. Thanks.
![[thumbsup] [thumbsup] [thumbsup]](/data/assets/smilies/thumbsup.gif)
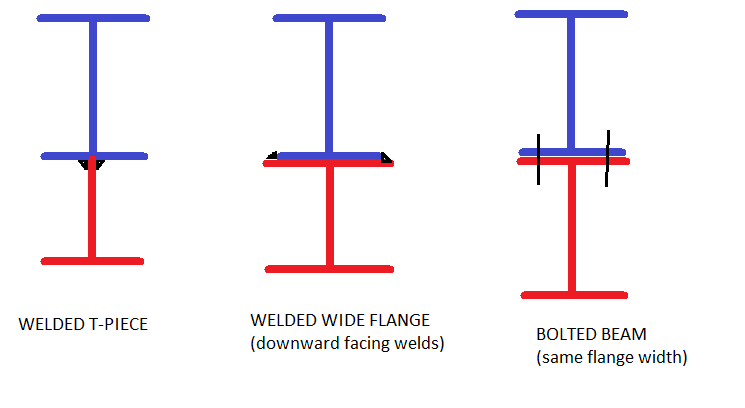