ClocksNbells
Structural
- May 11, 2016
- 2
I've designed a clamp-on saddle bracket that clamps to a vertical pole. See attachment.
There are four of these brackets for hanging large bells.
The Architects are asking for a "torque" required to safely secure these brackets to the pole.
Initially, I was going to suggest the "turn of the bolt" torque method. But if my thinking is correct this doesn't apply because my brackets have an open space. Thus all the "plies" will not contact each other.
So now, I'm at a bit of a loss.
Is my thinking correct on the "turn of the nut" method not being valid?
How do I determine the torque required to secure these brackets?
Thanks.
There are four of these brackets for hanging large bells.
The Architects are asking for a "torque" required to safely secure these brackets to the pole.
Initially, I was going to suggest the "turn of the bolt" torque method. But if my thinking is correct this doesn't apply because my brackets have an open space. Thus all the "plies" will not contact each other.
So now, I'm at a bit of a loss.
Is my thinking correct on the "turn of the nut" method not being valid?
How do I determine the torque required to secure these brackets?
Thanks.
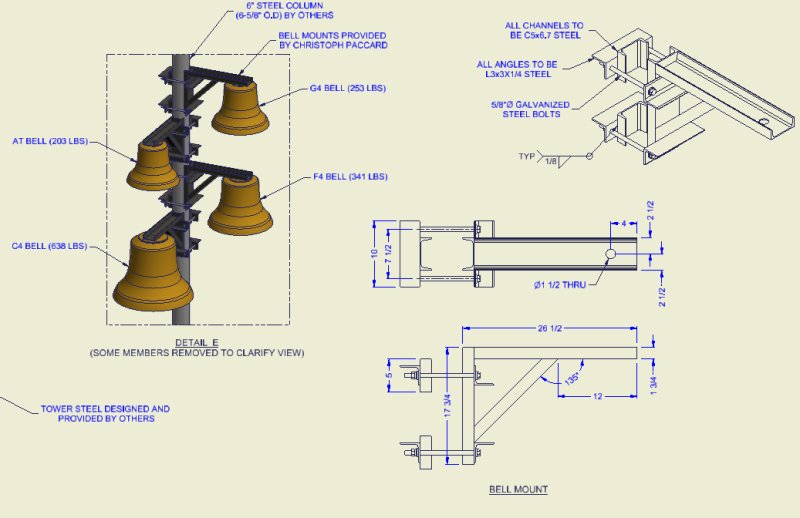