TRAK.Structural
Structural
- Dec 27, 2023
- 292
Working on a situation where I've got to raise the floor level in an existing depressed room at a residential property. It's old construction from the 60's. Existing floor is slab on grade of unknown thickness poured separate from the perimeter walls (floating slab). Perimeter walls in the space are (2) wythes of brick, with the outer course continuing up as the veneer. Foundation under the masonry walls is unknown. In the adjacent area that has a higher floor elevation, the 2x8 joists bear on top of the masonry stem wall, so I need to raise the floor to match. Debating whether I should just span new joists on top of the masonry stem which increases the load on unknown foundations............or make a couple short wood framed knee walls on top of the slab and support joists off those. It would make line loads on the slab but probably small enough magnitude to be ok. See image below, this is the depressed room, the stud walls are exterior and must remain. Any thoughts?
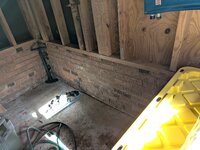
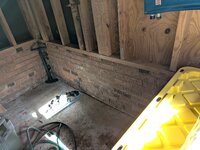