Need some advice from any Bridge Rating Engineers.
I am rating an existing bridge (4 Simple spans,rolled steel beams with a noncomposite concrete deck) which has a Shear connection (Web Splice plate only. No splice connection on the flanges) on the beams of one of the interior spans. It looks to be a construction error where the pier was off by few feet, so they added a Shear connection on the original beam length to make it work. The splice is located close to the support (3ft away from support on a 74ft beam span), so the behavior can be assumed to be as 2-Span continuous with a hinge at the splice location.
I analyzed and rated the beams using AASHTOWare. The Shear Forces at the hinge for various load conditions can be obtained from AASHTOWare and used to rate this Shear connection for:
► Connection Bolts in Shear and Bearing
► Flexural Yielding and Flexural Rupture of the Connection Plate due to the Eccentric moment from the applied Shear force
► Shear Yielding and Shear Rupture of the Connection Plate
► Block Shear and Tension Fracture of the Connection Plate
I could not find any examples using AASHTO Std Specs for Highway Bridges or in the MBE(Manual for Bridge Evaluation) to evaluate this connection using Allowable Stress (ASR).
Any suggestions or examples I could refer? I can get the necessary allowable stresses for plate and bolts from the MBE but not sure about the equations to be used to evaluate stresses due to the loads.
The bridge was originally designed using ASD and per State DOT's guideline we need to rate it using Allowable Stress.
Alternatively (Not the preferred option to avoid mixing different code provisions) I am familiar with evaluating the connection using AISC provisions, however I am not sure on how to consider the effects of mixing load factors and varying allowable stresses when mixing the two codes for evaluation. Any suggestions?
I am rating an existing bridge (4 Simple spans,rolled steel beams with a noncomposite concrete deck) which has a Shear connection (Web Splice plate only. No splice connection on the flanges) on the beams of one of the interior spans. It looks to be a construction error where the pier was off by few feet, so they added a Shear connection on the original beam length to make it work. The splice is located close to the support (3ft away from support on a 74ft beam span), so the behavior can be assumed to be as 2-Span continuous with a hinge at the splice location.
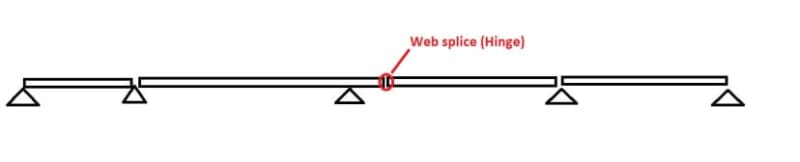
I analyzed and rated the beams using AASHTOWare. The Shear Forces at the hinge for various load conditions can be obtained from AASHTOWare and used to rate this Shear connection for:
► Connection Bolts in Shear and Bearing
► Flexural Yielding and Flexural Rupture of the Connection Plate due to the Eccentric moment from the applied Shear force
► Shear Yielding and Shear Rupture of the Connection Plate
► Block Shear and Tension Fracture of the Connection Plate
I could not find any examples using AASHTO Std Specs for Highway Bridges or in the MBE(Manual for Bridge Evaluation) to evaluate this connection using Allowable Stress (ASR).
Any suggestions or examples I could refer? I can get the necessary allowable stresses for plate and bolts from the MBE but not sure about the equations to be used to evaluate stresses due to the loads.
The bridge was originally designed using ASD and per State DOT's guideline we need to rate it using Allowable Stress.
Alternatively (Not the preferred option to avoid mixing different code provisions) I am familiar with evaluating the connection using AISC provisions, however I am not sure on how to consider the effects of mixing load factors and varying allowable stresses when mixing the two codes for evaluation. Any suggestions?