FreshGenZSE
Structural
- Oct 30, 2024
- 5
Hello Engineers,
First time posting and keen to get some design advices. Please see query as below.
Question:
I have an octagonal footing foundation design for wind turbines. What is the rationale of not having the stirrups (light blue) continuing into the “x” region marked in purple shown in the attached cross-section, 3 m thick?
For illustration purpose, please see the sketch below.
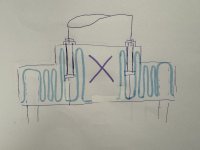
The governing shear force diagram is as below.
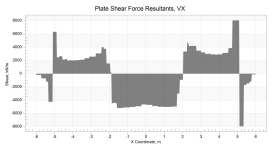
I say to provide stirrups myself but open to discussion as I may be overly conservative! Note that the shear demand is significantly larger than the concrete strength and the wind turbine tower is hollow.
Reason(s):
Thanks in advance.
First time posting and keen to get some design advices. Please see query as below.
Question:
I have an octagonal footing foundation design for wind turbines. What is the rationale of not having the stirrups (light blue) continuing into the “x” region marked in purple shown in the attached cross-section, 3 m thick?
For illustration purpose, please see the sketch below.
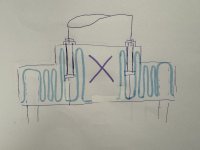
The governing shear force diagram is as below.
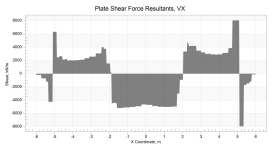
I say to provide stirrups myself but open to discussion as I may be overly conservative! Note that the shear demand is significantly larger than the concrete strength and the wind turbine tower is hollow.
Reason(s):
- I have seen similar details in different projects with only mass concrete in the same region. I pointed it out to my manager and colleagues. They do believe it should be provided, but have no answer to my query so far.
- I am uncomfortable to make the additional depth assumption as the tower is a hollow section. I am also recommended the same as it could be a risky call.
- I have attempted to use strut-and-tie to justify that diagonal strut is viable alone. I resolved the overturning moment into axial tension and compression at the bolt connection, but found it impossible to have no tie in the region while having a model that is structurally stable!
Thanks in advance.