milkshakelake
Structural
Question:
Why do some engineers use significantly longer 90 degrees hook lengths than is required by ACI code? For example, having the leg be 24" long for #5 bar, when only 10" is needed.
Background:
Per ACI 318-14,
So #5 needs 10". This is also shown in CRSI manual. However, I've seen two different firms use 24" for both #4 and #5. It seems excessive. I think there must be a reason for it, like it's easier to cut or something. Or maybe it's a regional thing, where "my grandfather did it this way for 1000 years" so everyone does it. I'm in the east coast.
Why do some engineers use significantly longer 90 degrees hook lengths than is required by ACI code? For example, having the leg be 24" long for #5 bar, when only 10" is needed.
Background:
Per ACI 318-14,
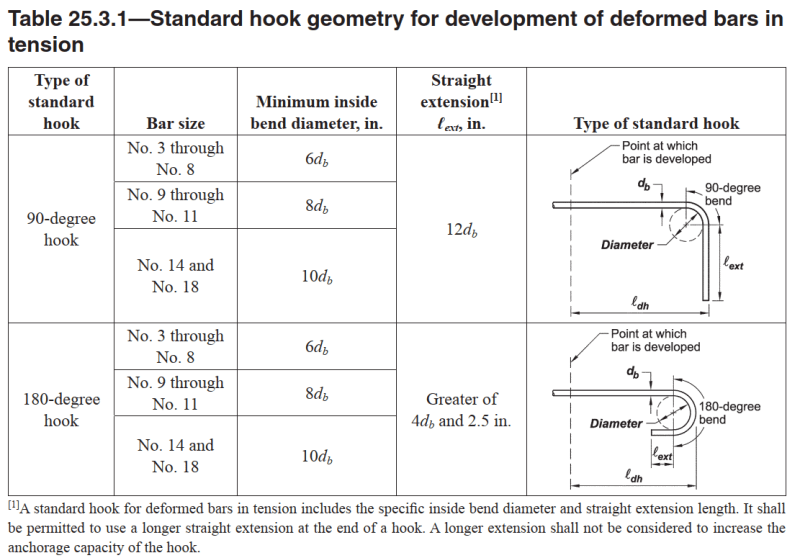
So #5 needs 10". This is also shown in CRSI manual. However, I've seen two different firms use 24" for both #4 and #5. It seems excessive. I think there must be a reason for it, like it's easier to cut or something. Or maybe it's a regional thing, where "my grandfather did it this way for 1000 years" so everyone does it. I'm in the east coast.