As you can see the following details, the base plate is connected to the concrete through rebars instead of J/L bolts. I am wondering if I can assume it is a L/J bolt in my calculation with the same diameter. The rebar strength is 60ksi. Welding is a more widespread practice in my city but I am concerned about brittleness in that area. But maybe I am overthinking this. What are your thoughts? Thank you!
Edit: typo
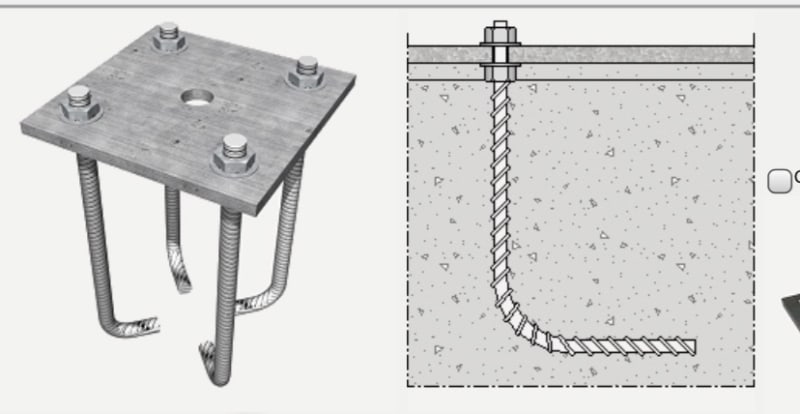
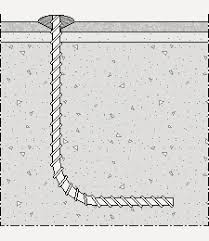
Edit: typo