dejan95
Mechanical
- Aug 24, 2020
- 60
Hello everybody.
I'm a fresh mechanical engineer, only been working for a good two months in mechanical design.
For my new project I got instructions to reduce mass of a cover for guide pulley on the belt unwinder. Every time the belt needs to be replaced, the worker has to take of the cover (12kg) which is not an easy task. I would like to reduce the weight of the cover to at least 6 kg.
Additionally I would love to make easier/quicker locking system.
Things I considered regarding weight:
- making parts from aluminium to reduce some weight;
- reducing the diameter from 1070 mm to 950 mm (it would still serve the same propose);
- reducing the thickness from 3mm to 2 mm.
I have attached some additional pictures for better understanding.
I would really appreciate some help from you more experienced engineers.
I'm a fresh mechanical engineer, only been working for a good two months in mechanical design.
For my new project I got instructions to reduce mass of a cover for guide pulley on the belt unwinder. Every time the belt needs to be replaced, the worker has to take of the cover (12kg) which is not an easy task. I would like to reduce the weight of the cover to at least 6 kg.
Additionally I would love to make easier/quicker locking system.
Things I considered regarding weight:
- making parts from aluminium to reduce some weight;
- reducing the diameter from 1070 mm to 950 mm (it would still serve the same propose);
- reducing the thickness from 3mm to 2 mm.
I have attached some additional pictures for better understanding.
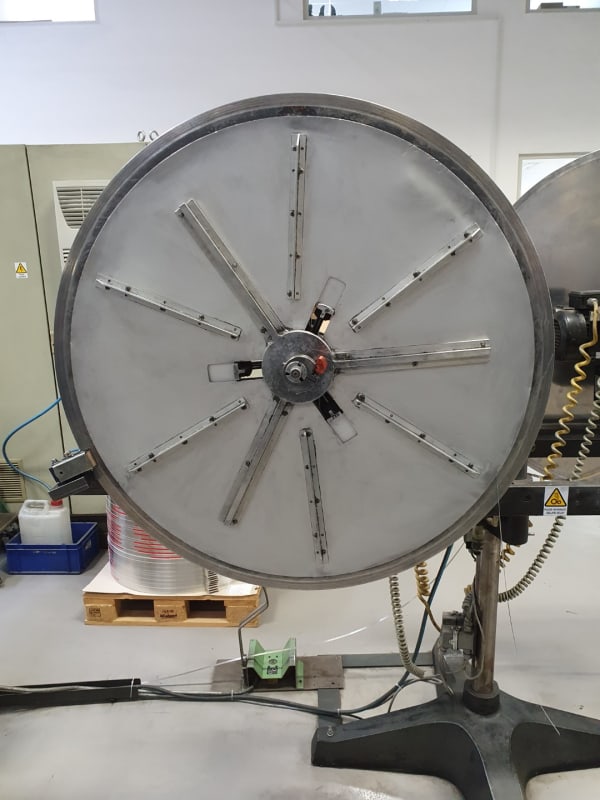
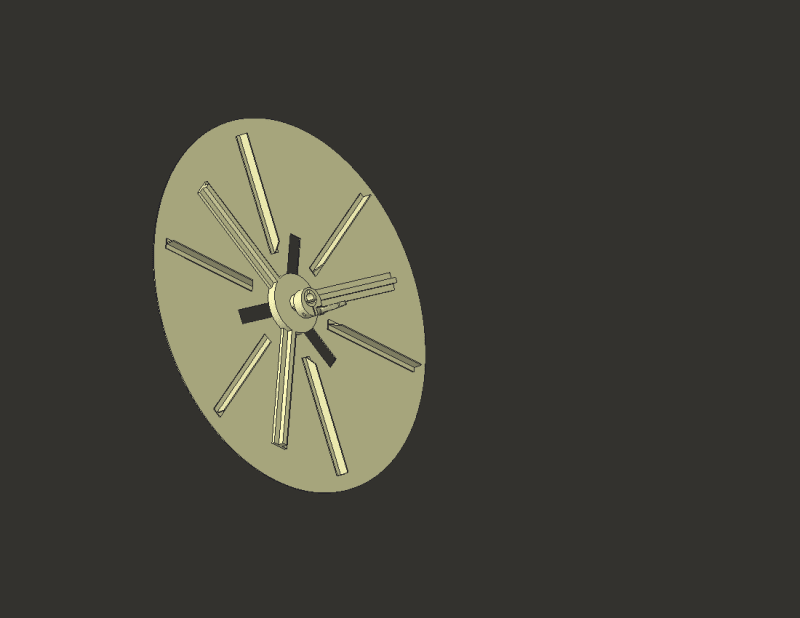
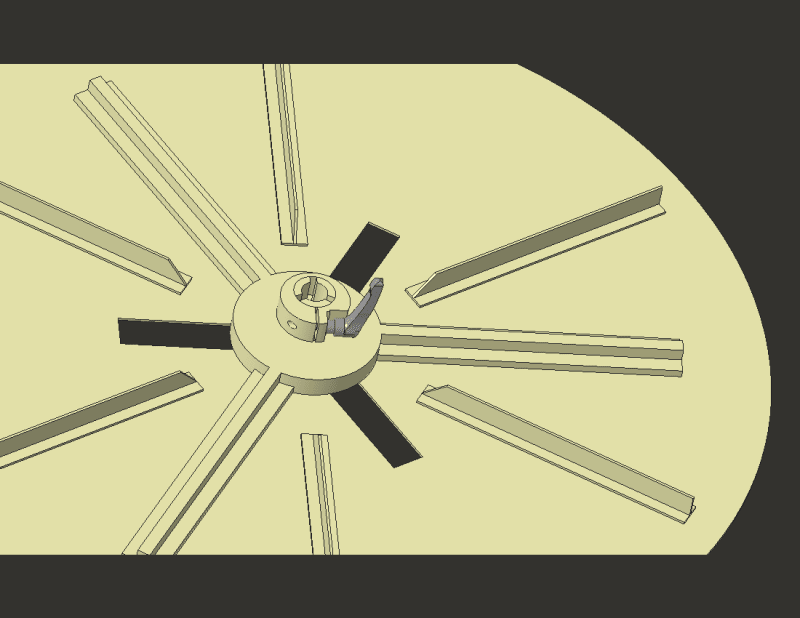
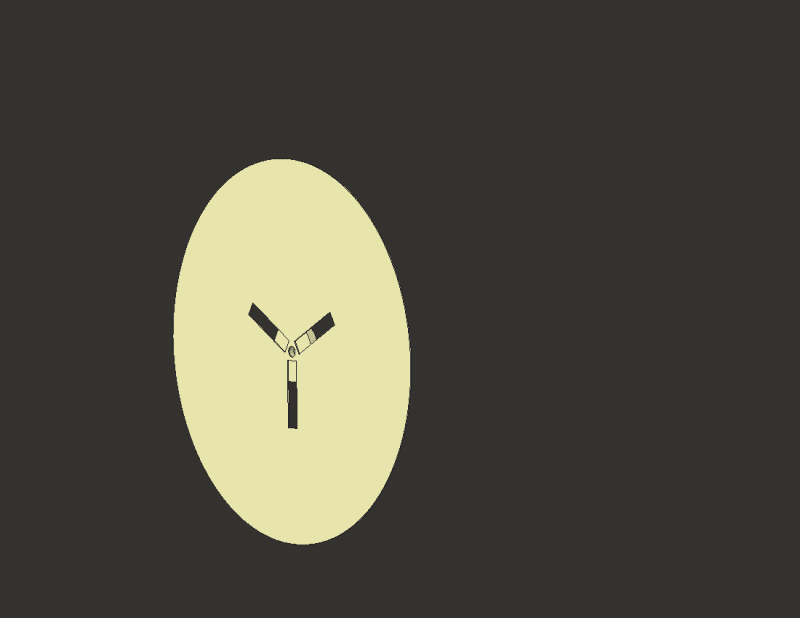
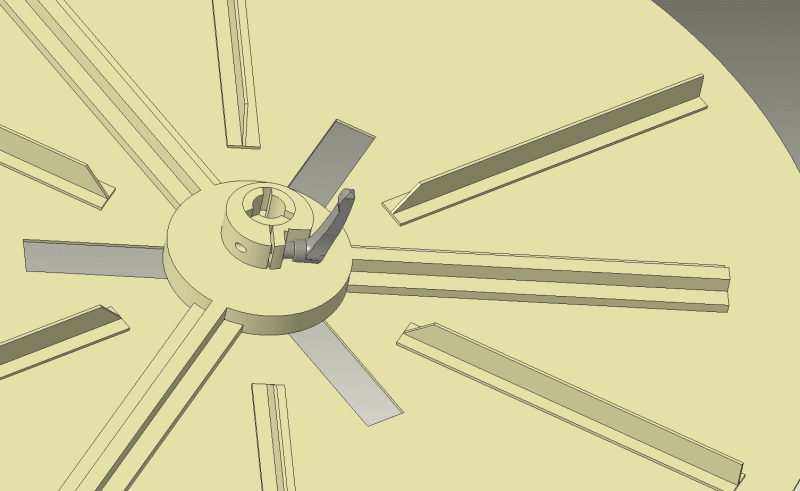
I would really appreciate some help from you more experienced engineers.