A client is placing a new RTU on two existing composite trusses. The trusses are in the style of the Redbuilt "Red-L" trusses, with wood top and bottom chords and steel webs. The building is from the 50's or 60's, so I believe the trusses were likely manufactured by Weyerhauser before they sold off this product to Redbuilt. Speaking with a rep from Redbuilt, these trusses were likely designed to be fully utilized, and adding any additional weight would overload them.
My question is whether reinforcing these trusses should be something we consider, or if we should add new support to take the RTU load separately from the existing structural elements? How would you reinforce this style of truss? Our initial thought was to stack an additional ply below the bottom chord, and add LVL's to either side of the top chord, but the connection may be an issue and this doesn't reinforce the webs, if that is required.
My question is whether reinforcing these trusses should be something we consider, or if we should add new support to take the RTU load separately from the existing structural elements? How would you reinforce this style of truss? Our initial thought was to stack an additional ply below the bottom chord, and add LVL's to either side of the top chord, but the connection may be an issue and this doesn't reinforce the webs, if that is required.
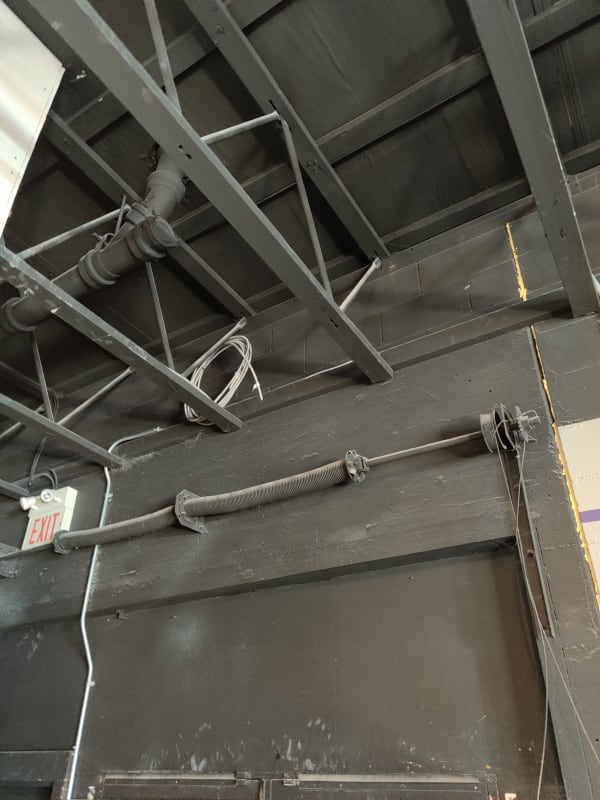