tmgczb
Structural
- May 12, 2021
- 174
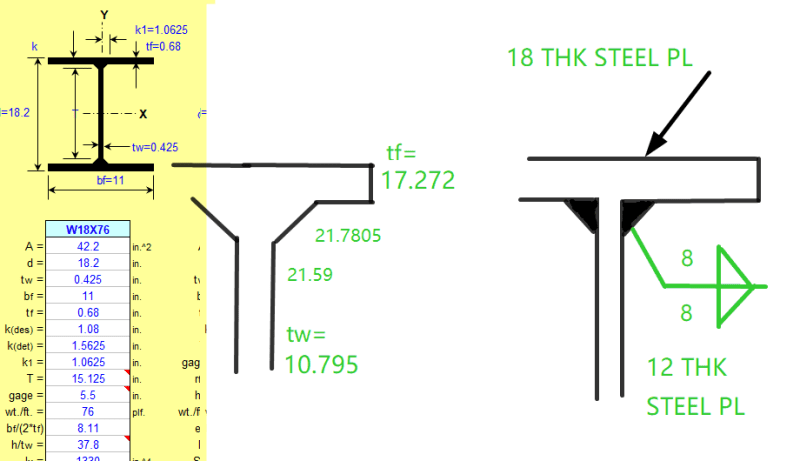
I have no experience nor knowledge of
Now vendor for our project is suggesting that we replace W18x76 with a built up section.
The thickness of steel plates is 18mm and 12mm, connected by fillet weld 8mm at both sides of web plate.