Hi every one
Recently I tried to make a Laminar box that composed several layers. and layers must have moving freedom in X (Longitudinal) direction under load.
to reach this goal I made some Aluminium frames and put flat bearing between layers.
But when I applied load on frames, they Locked and didn't move at all .
why this happend ?
Recently I tried to make a Laminar box that composed several layers. and layers must have moving freedom in X (Longitudinal) direction under load.
to reach this goal I made some Aluminium frames and put flat bearing between layers.
But when I applied load on frames, they Locked and didn't move at all .
why this happend ?
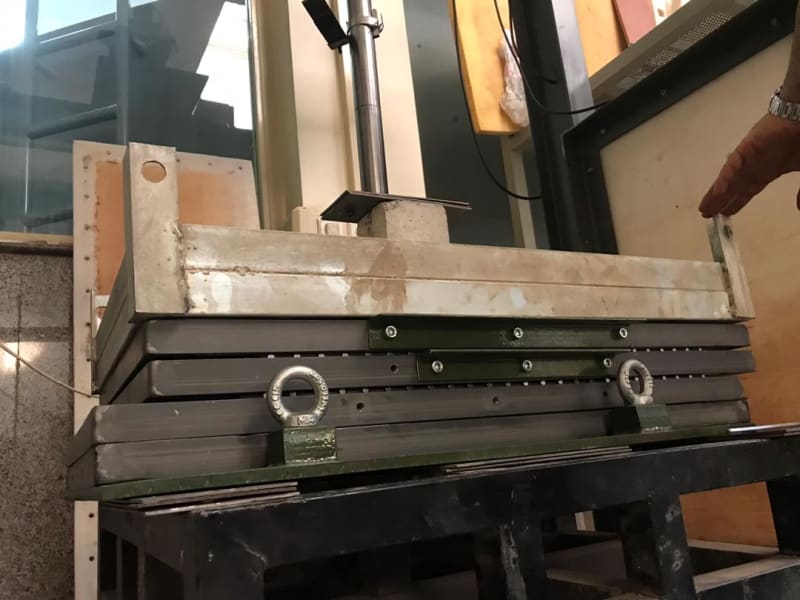