Hello all,
i am working on a girder beam(1000X420X40X32) to column web(25mm) connection with a big shear load(500KN) and transfer load(+/- 1000KN). i am using shear end plate (32mm) to transfer the load. a very thick endplate needed after considering prying action( M20 steel bolt is used). I have a little concern about the rotation ability for the girder beam as the end plate is too thick.it may become a semi-rigid connection which can take some moment which i don't expect to see. but from another side it seems impossible to use a thin end plate due to the heavy section and big design load. i am wondering who can give some suggestion and opinions for this detail? i attached the detail for detail information. and are there any good articles addressing end plate connection rotation ability?
thank you!
i am working on a girder beam(1000X420X40X32) to column web(25mm) connection with a big shear load(500KN) and transfer load(+/- 1000KN). i am using shear end plate (32mm) to transfer the load. a very thick endplate needed after considering prying action( M20 steel bolt is used). I have a little concern about the rotation ability for the girder beam as the end plate is too thick.it may become a semi-rigid connection which can take some moment which i don't expect to see. but from another side it seems impossible to use a thin end plate due to the heavy section and big design load. i am wondering who can give some suggestion and opinions for this detail? i attached the detail for detail information. and are there any good articles addressing end plate connection rotation ability?
thank you!
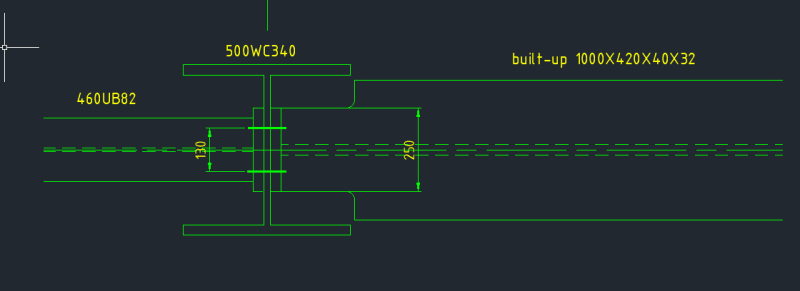
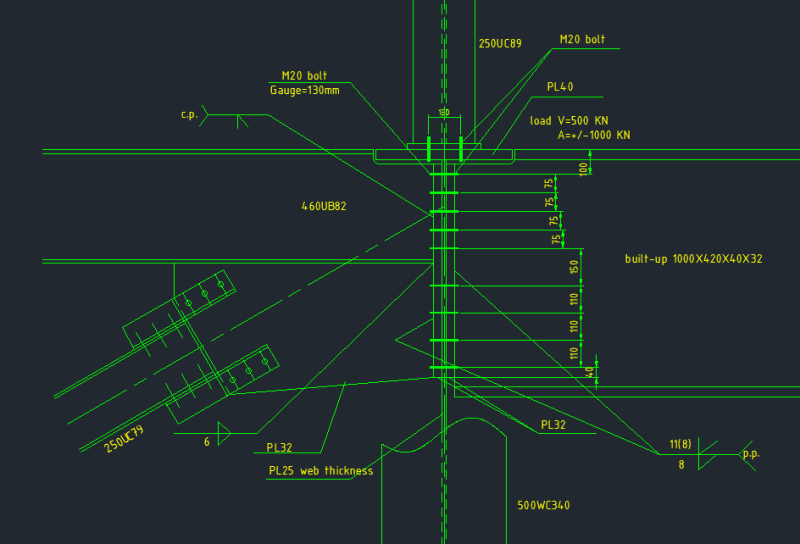