bridgebuster
Active member
- Jun 27, 1999
- 3,969
I'm looking at the design of a structure that will temporarily support a section of a viaduct while the structure it normally rests on is being replaced; illustration below. The pier columns are round HSS. The designer used a k factor of 0.8. In my mind k should be well north of 1.0. To me it's a frame with side sway in the direction of the bridge. The girders simply sit on the pier cap beam and are held with two bolts. I was wondering what others think. I have to post another illustration to provide further clarity.
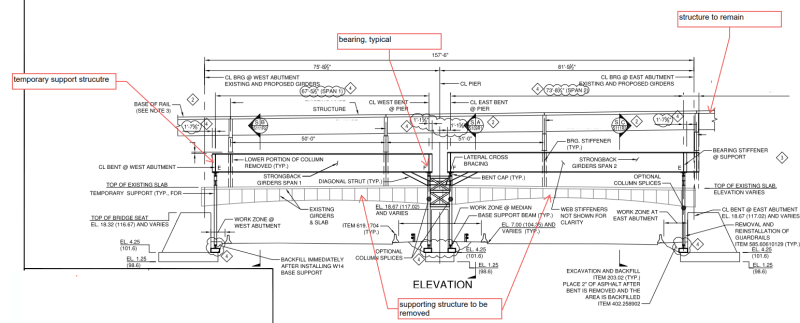