greenimi
Mechanical
- Nov 30, 2011
- 2,391
Why runout is used in this figure? (instead of profile)
What would be the difference between using profile (maybe even with dynamic profile modifier) instead of currently shown total runout?
Are there any mathematical difference between shown total runout and profile (again with dynamic profile maybe) ?
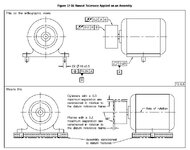
What would be the difference between using profile (maybe even with dynamic profile modifier) instead of currently shown total runout?
Are there any mathematical difference between shown total runout and profile (again with dynamic profile maybe) ?
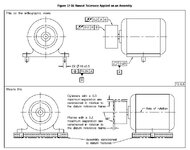