BEMPE16524
Mechanical
I just want to share with all how safety is very important.
We were instructed to service an old hydraulic cylinder from one Client XXX. The working pressure is 250 Bar and test to 1.5 times.
During extend, at around 320-350 Bar, BANG!!!
The gland pop out. The thread were sheared off. Luckily no incident.
Now, for the next test after re-pair, need to add more safety features. Thinking of covering the perimeter with solid counter weight.
We were instructed to service an old hydraulic cylinder from one Client XXX. The working pressure is 250 Bar and test to 1.5 times.
During extend, at around 320-350 Bar, BANG!!!
The gland pop out. The thread were sheared off. Luckily no incident.
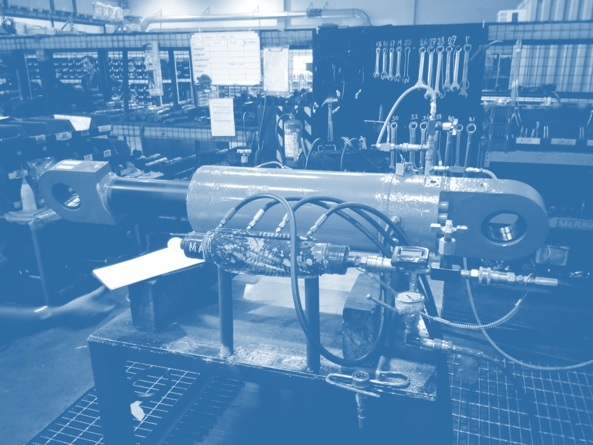
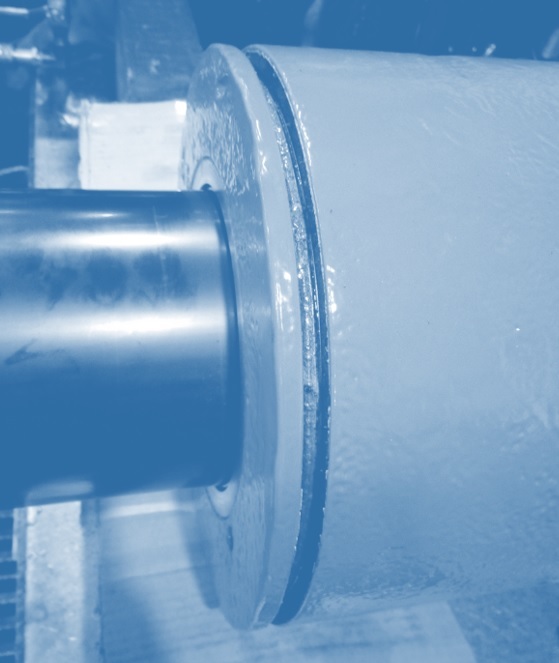
Now, for the next test after re-pair, need to add more safety features. Thinking of covering the perimeter with solid counter weight.