gersen
Materials
- Nov 14, 2017
- 27
Hello,
recently I had the a problem with a bolted flange. After a repair some of the screw head pop out (see the picture below).
Is it possible that the failure is due to a too high torque during bolting-up?
All the damaged screw broke at the base of the head.
The screw are Socket Head Cap M24 class 12.9, they bolted them with 2 (don't know why) split-lock washer DIN 127 B.
recently I had the a problem with a bolted flange. After a repair some of the screw head pop out (see the picture below).
Is it possible that the failure is due to a too high torque during bolting-up?
All the damaged screw broke at the base of the head.
The screw are Socket Head Cap M24 class 12.9, they bolted them with 2 (don't know why) split-lock washer DIN 127 B.
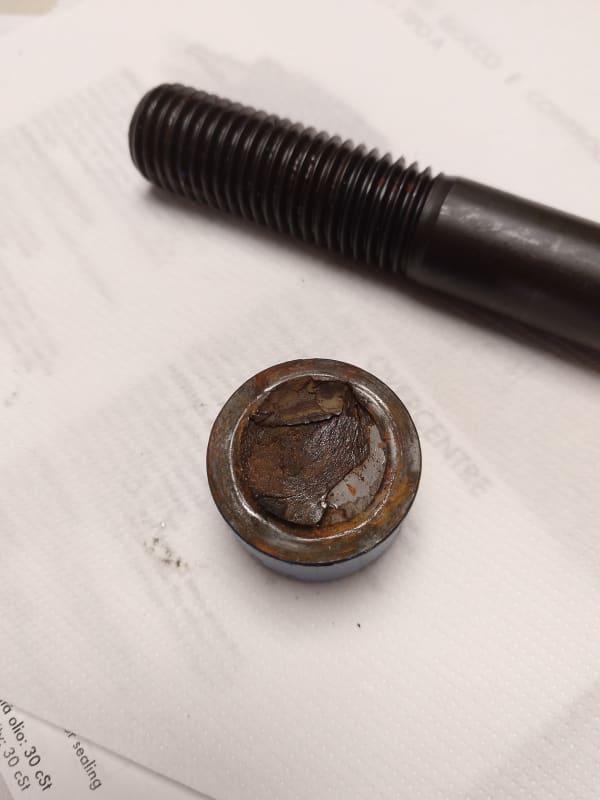
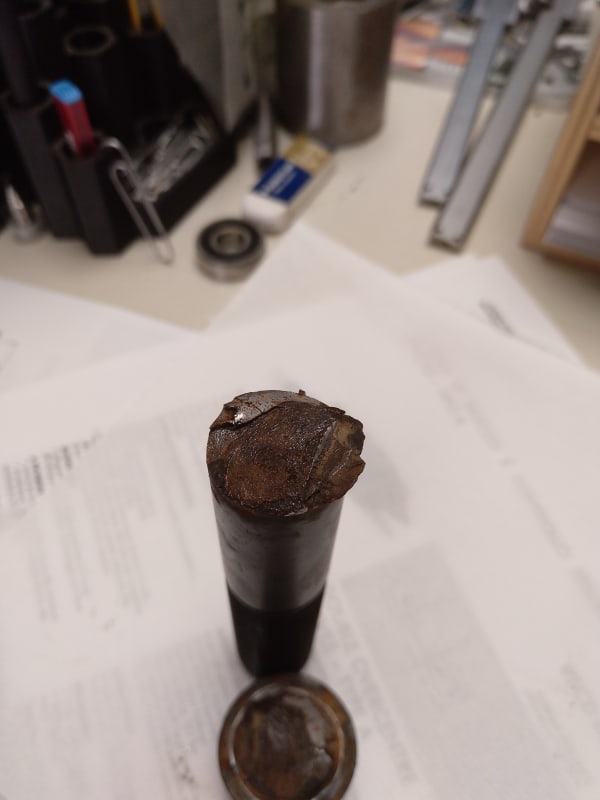