hi,
We have a screw-plug(forgive me my poor English) fractured after about one year in use. the location of the fracture is at the fillet . after disassemnlying the transmission, it was found that the screw thread was completely stripped out as the below photo shows(this is another failed part, and is similar with the fractured one).
Below photo shows you the fracture surface and the assembly schematic diagram.
The fractured part’s microstructure,HV and its tightening curve were all examined ,and all of them are OK. and also no decarburization was detected.
my question is how this failure happened and what made the screw thread stripped? Can anyone give me some light on it and request your suggestion.
thanks in advance.
We have a screw-plug(forgive me my poor English) fractured after about one year in use. the location of the fracture is at the fillet . after disassemnlying the transmission, it was found that the screw thread was completely stripped out as the below photo shows(this is another failed part, and is similar with the fractured one).
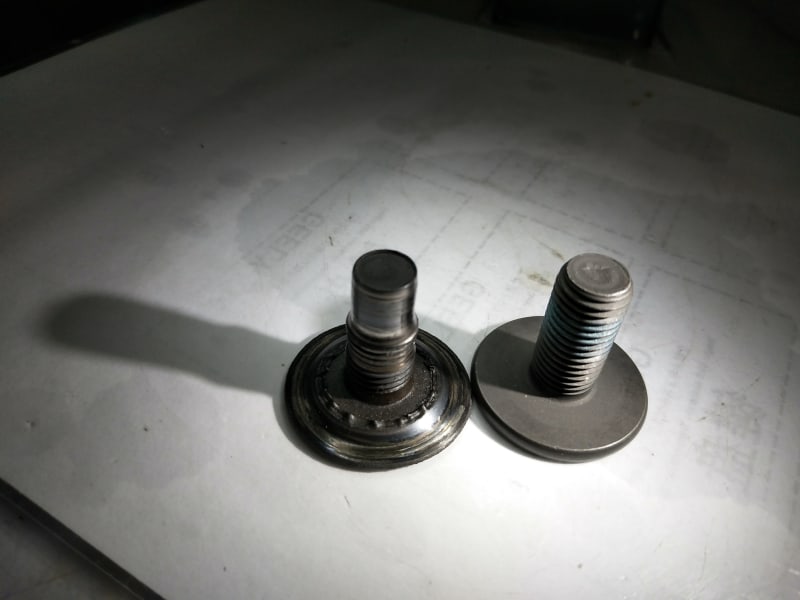
Below photo shows you the fracture surface and the assembly schematic diagram.
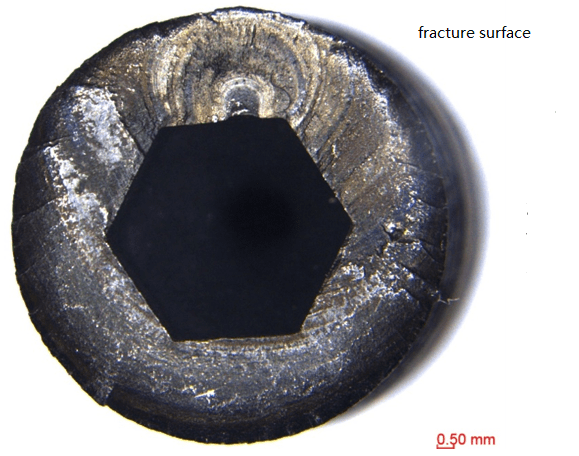
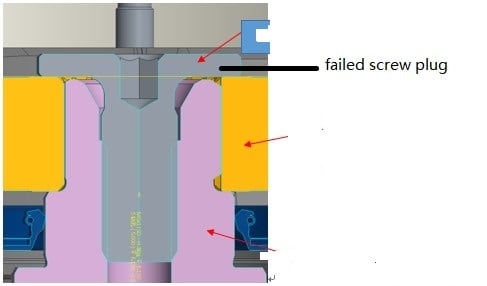
The fractured part’s microstructure,HV and its tightening curve were all examined ,and all of them are OK. and also no decarburization was detected.
my question is how this failure happened and what made the screw thread stripped? Can anyone give me some light on it and request your suggestion.
thanks in advance.