lucky-guesser
Industrial
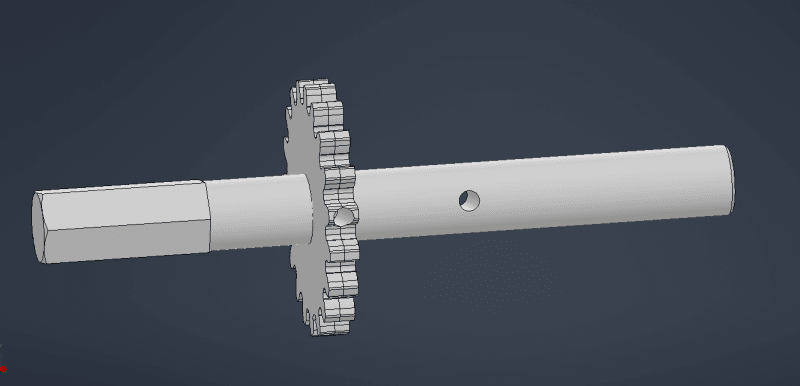
I am working on a functioning prototype that is very similar to what the final result will be. You can see in the attached image, my gear laminates that would be braze welded together, are drilled through so that a small roll pin can fix them to the shaft during assembly. Some time later the caffeine kicked in and I realized what a nightmare this hole will be to drill. By that point I had already designed the entire rest of the assembly around this drive shaft, so my options are limited on what changes I can make. The task at hand is that I need a way to attach these gears (will likely be a single thicker gear in production) using some method that can be done during final assembly with hand tools. Using a key seems easy, except I have a bearing directly on either side of the gears so the key can only be cut as wide as the gear thickness, and I've never seen it done like that. 5/8 dia shaft, gears are roughly 1/4 thick total.
If a redesign is in order then it is what it is but after the latest department meeting everyone liked this design, minus the obvious flaw, so I am hesitant to change more than I have to.