StrEng007
Structural
- Aug 22, 2014
- 543
According to ACI 318-19, it is necessary to check shear friction at locations of potential cracks. This includes monolithic pours.
I typically check the ends of my monolithic beams for shear using Vn = Vc + Vs. If required, I provide shear steel in the form of vertical stirrups to resist diagonal tension.
I always extend my bottom bars into the column supports, but I don't go out of the way to check shear friction unless it's a 2nd pour at a cold joint. Does everyone do the shear friction check at monolithic pours?
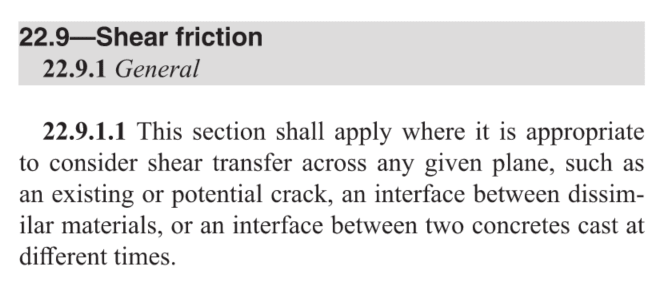
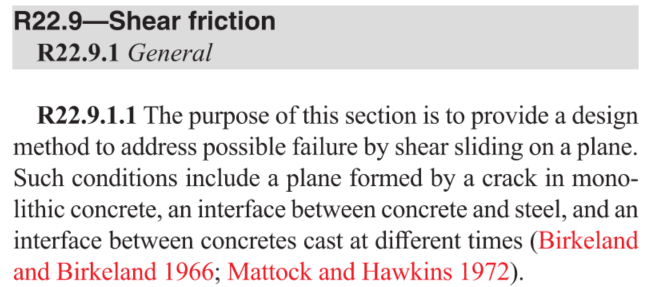
I typically check the ends of my monolithic beams for shear using Vn = Vc + Vs. If required, I provide shear steel in the form of vertical stirrups to resist diagonal tension.
I always extend my bottom bars into the column supports, but I don't go out of the way to check shear friction unless it's a 2nd pour at a cold joint. Does everyone do the shear friction check at monolithic pours?