If you have a long plate (Plate 1) that is in tension, with a force of Pu (factored) and you need to occasionally have a splice in it to limit the length of plates needed in the field, and if you used a perpendicular splice plate as shown in the attached image, how would you treat the issue of shear lag in the splice Plate 2?
AISC has table D3.1, which provides various U values to reduce the effective area of the plate when checking a plate's tension capacity.
This takes the form of ΦPn = ΦAe(Fy)U.
However, table D3.1 doesn't seem to include this particular condition.
Case 2, which includes the U = 1 - x/L specifically omits plates.
Case 3 is for transverse welds, not longitudinal.
Case 4 seems to apply to a plate with longitudinal welds on both sides of the plate – not on just one side.
The other cases are all totally different conditions.
Any thoughts?
Check out Eng-Tips Forum's Policies here:
faq731-376
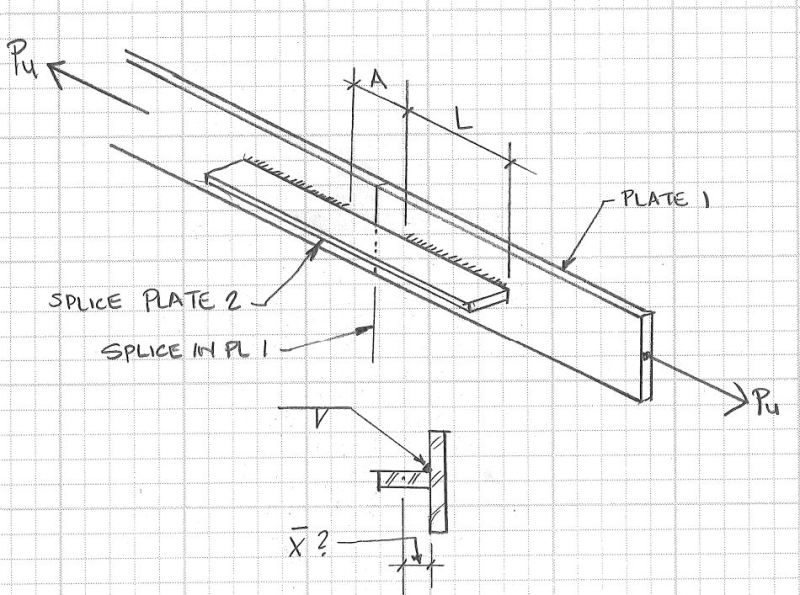
AISC has table D3.1, which provides various U values to reduce the effective area of the plate when checking a plate's tension capacity.
This takes the form of ΦPn = ΦAe(Fy)U.
However, table D3.1 doesn't seem to include this particular condition.
Case 2, which includes the U = 1 - x/L specifically omits plates.
Case 3 is for transverse welds, not longitudinal.
Case 4 seems to apply to a plate with longitudinal welds on both sides of the plate – not on just one side.
The other cases are all totally different conditions.
Any thoughts?
Check out Eng-Tips Forum's Policies here:
faq731-376