Mike Mike
Structural
- Apr 27, 2019
- 140
Hi all, what is the minimum weld length for tension members? We are designing a ton of welded knife plate connections for HSS10x10x1/4 tension and compression braces. The LRFD tensile capacity is 371k. The LRFD axial load is +-100k, so we only need (4) 6" long 3/16" fillet welds, and we only need a U factor of around 0.27. But to comply with case 6 in the table below, we have to specify 10" minimum. Why does the table state l >= H? Were shorter welds not tested? Would you be comfortable pushing this recommendation? It seems we have mixed opinions in my office.
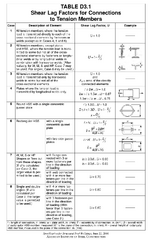
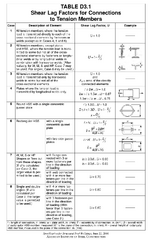