Hi everyone,
At the company I work for (design and construct shoring wall contractor) it is common to implement a corner brace for , say, a sheet pile wall.
Analyzing the system in 2d is simple: prop forces, embedment, wall forces etc. However I cannot find any guidance on how to resolve the load transferred into the the 'shear wall'.
The more senior people designing this also have no idea either - just that "it cant fail like that".
Any ideas/comment?
At the company I work for (design and construct shoring wall contractor) it is common to implement a corner brace for , say, a sheet pile wall.
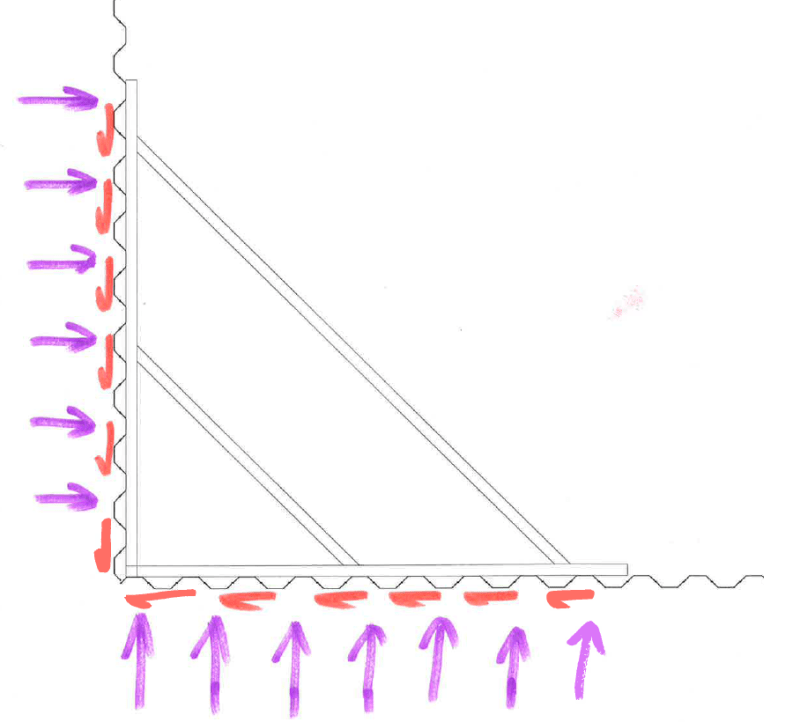
Analyzing the system in 2d is simple: prop forces, embedment, wall forces etc. However I cannot find any guidance on how to resolve the load transferred into the the 'shear wall'.
The more senior people designing this also have no idea either - just that "it cant fail like that".
Any ideas/comment?