Nice little problem for you al1!
We have a 1965 British built by W H allen v16 large generating set that has just been saved for preservation. The complete set up is in very good condition having only done about 2600 hours. We have the complete contents of the generator building to include all the switchgear etc. This engine represents a British engine manufacturer and a early type of large packaged generator.
it also has open rocker gear which will be very nice to watch.
The alternator is a brushless type with the supply for the AVR being picked up via a 6.6kv/110volt voltage transformer. There must be an element of self exciting on start up?
The alternator was wired in star with the centre point earthed via a neutral resistor which we were unable to obtain due to asbestos content within the resistors housing.
The alternator details are
1666kva
1333kw
rpm 750
power factor 0.8
volts 6600
amps 145.7
Brushless a.c exciter details
kw (dc) 16.45
volts (dc) 82
amps (dc) 201
poles 6
3 phase
frequency 37.5
full load exciter ac voltage 49.4
ac current 6.13
rectifier connection. 3 phase bridge.
The engine is in perfect condition and within a few months this will be back fully operational after reconnecting the shut downs and control circuits which have been a total joy to work on due to their age.
I fully appreciate it is both impractical and unsafe to even think about returning the alternator to service plus to have the ability to load up this engine with a load bank, the resources involved and expenditure would be too great.
But...........
It would be good however, to place a load on this engine even if it is nowhere near to the full capacity of the alternator.
So here is the question: Thinking outside of the box do any of you think this alternator could be wired to give some sort of load.....such as windings shorted, d.c injection etc etc. basically anything that will cause a load to the prime mover without having to generate at the full voltage. I suppose the major problem is the flc current, as we reduce the voltage to a safe level the 145 odd amps on a 2000 hp diesel engine, it wont even know it is there! but I do not know about any other methods that could be used that are either used for testing purposes or a alternative radical approach.
Any ideas or do you think it is impractical and wont actually generate any sort of engine load,
I have attached some pictures of the generator that was saved, ironically from Astra Zenica early last year. Little did we know what was about to come.
Cheers
M
ark
We have a 1965 British built by W H allen v16 large generating set that has just been saved for preservation. The complete set up is in very good condition having only done about 2600 hours. We have the complete contents of the generator building to include all the switchgear etc. This engine represents a British engine manufacturer and a early type of large packaged generator.
it also has open rocker gear which will be very nice to watch.
The alternator is a brushless type with the supply for the AVR being picked up via a 6.6kv/110volt voltage transformer. There must be an element of self exciting on start up?
The alternator was wired in star with the centre point earthed via a neutral resistor which we were unable to obtain due to asbestos content within the resistors housing.
The alternator details are
1666kva
1333kw
rpm 750
power factor 0.8
volts 6600
amps 145.7
Brushless a.c exciter details
kw (dc) 16.45
volts (dc) 82
amps (dc) 201
poles 6
3 phase
frequency 37.5
full load exciter ac voltage 49.4
ac current 6.13
rectifier connection. 3 phase bridge.
The engine is in perfect condition and within a few months this will be back fully operational after reconnecting the shut downs and control circuits which have been a total joy to work on due to their age.
I fully appreciate it is both impractical and unsafe to even think about returning the alternator to service plus to have the ability to load up this engine with a load bank, the resources involved and expenditure would be too great.
But...........
It would be good however, to place a load on this engine even if it is nowhere near to the full capacity of the alternator.
So here is the question: Thinking outside of the box do any of you think this alternator could be wired to give some sort of load.....such as windings shorted, d.c injection etc etc. basically anything that will cause a load to the prime mover without having to generate at the full voltage. I suppose the major problem is the flc current, as we reduce the voltage to a safe level the 145 odd amps on a 2000 hp diesel engine, it wont even know it is there! but I do not know about any other methods that could be used that are either used for testing purposes or a alternative radical approach.
Any ideas or do you think it is impractical and wont actually generate any sort of engine load,
I have attached some pictures of the generator that was saved, ironically from Astra Zenica early last year. Little did we know what was about to come.
Cheers
M
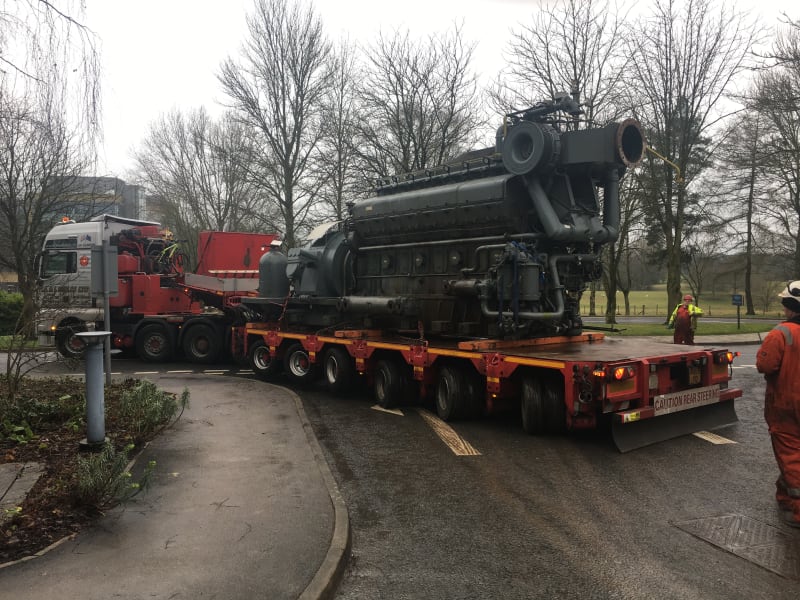
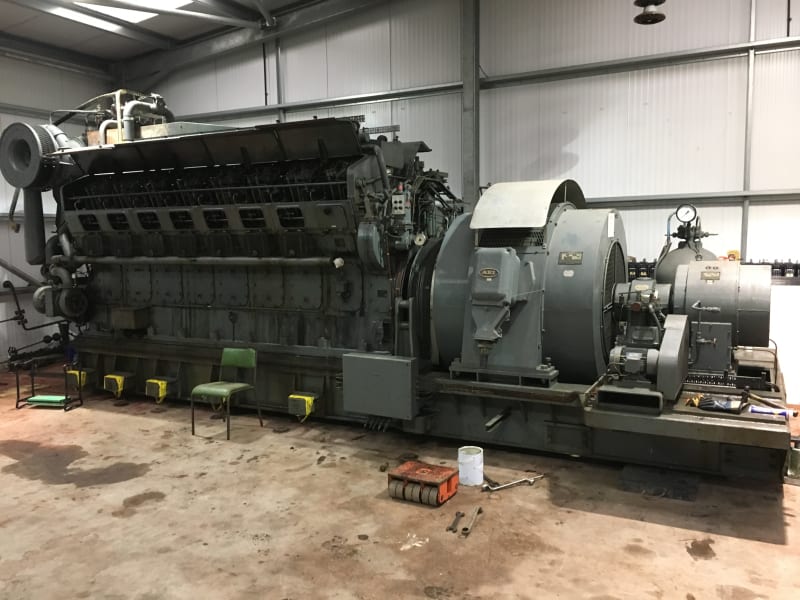