RabitPete
Structural
- Nov 24, 2020
- 109
I could not find any code reference to the minimum fillet size when designing coped beams. Which version on the pic below do you guys like more? Those are normally laser or plasma cut from 2 directions, so they rarely match perfect and typically leave some stress concentrators anyway
And sort of unrelated question: I was inspecting one of the projects last week and noticed that steel erector was cleaning off the shop coat on the mating surfaces, they told me its to improve electrical contact. Never seen it done before, does it really make any difference since some of it gets scratched anyway, especially under fasteners, and would not it be detrimental to corrosion protection?
And sort of unrelated question: I was inspecting one of the projects last week and noticed that steel erector was cleaning off the shop coat on the mating surfaces, they told me its to improve electrical contact. Never seen it done before, does it really make any difference since some of it gets scratched anyway, especially under fasteners, and would not it be detrimental to corrosion protection?
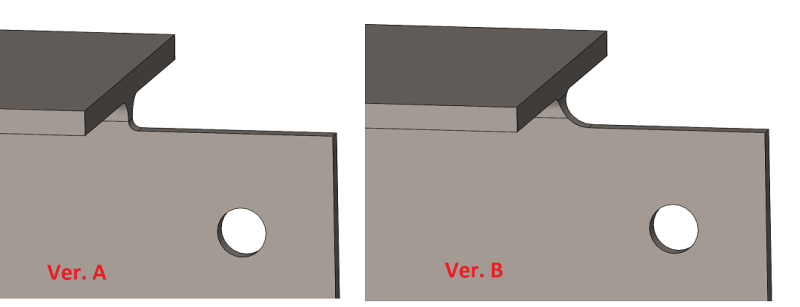