LexW.
Structural
- Nov 10, 2023
- 4
I have recently been assigned a project involving the design of new bottom pin connections for sliding aircraft doors to replace some of the existing ones that are old and damaged. The doors are 48m long and 16m high, with articulated joints located at 1/3 and 2/3 of their length. Each articulated joint comprises a bottom and top connection. The client specifically wants to change the bottom pin connections. The original ones consist of two L-shaped steel sections that are either bolted or welded to each side of the door structure, and a dowel in the middle slides through a slotted bolt hole in the top L (refer to below pictures for clarification).
Initially, I thought these connections served to transfer transverse load from one panel to the other, and that the impact of force transfer was causing damage to the existing connections. However, my perspective changed after observing the door in operation. It appears that the load transfers through the top connection exclusively. The dowel of the bottom joint moves 1/2 inch parallel to the doors but does not transfer any load between the door panels (no contact between the two L sections).
The challenge I'm facing is understanding the purpose of these connections in order to design new ones. The damaged ones seem to have been installed in the years after the construction of the doors. The L sections on the "newer" connections lack slotted holes in the top angle, which may have caused the observed damage during maintenance when portions of the doors were lifted (refer to pictures for clarification).
If anyone has experience in designing aircraft hangar doors and can provide insight into the purpose of these connections, it would be greatly appreciated.
Thank you.
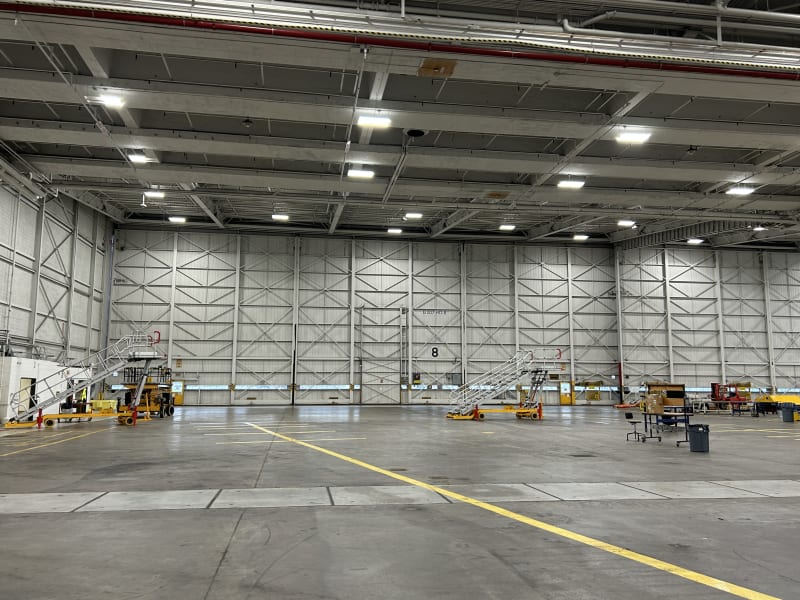
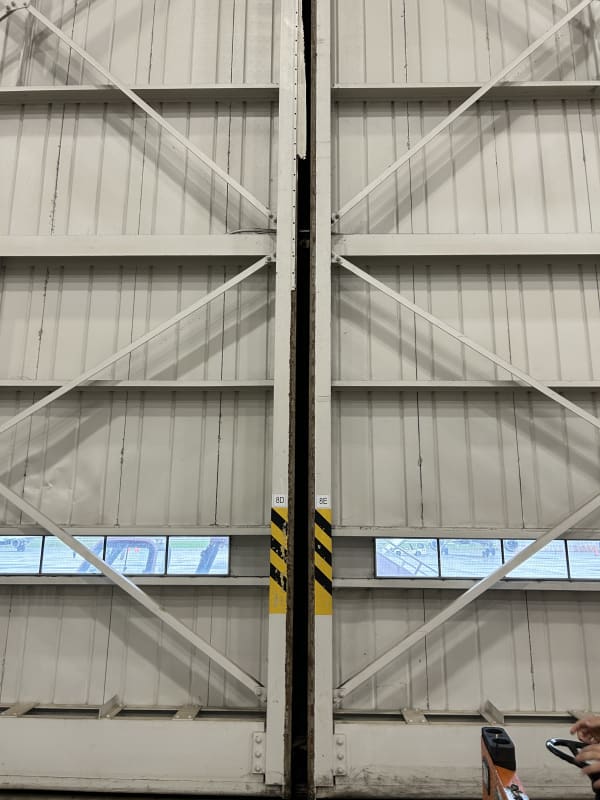
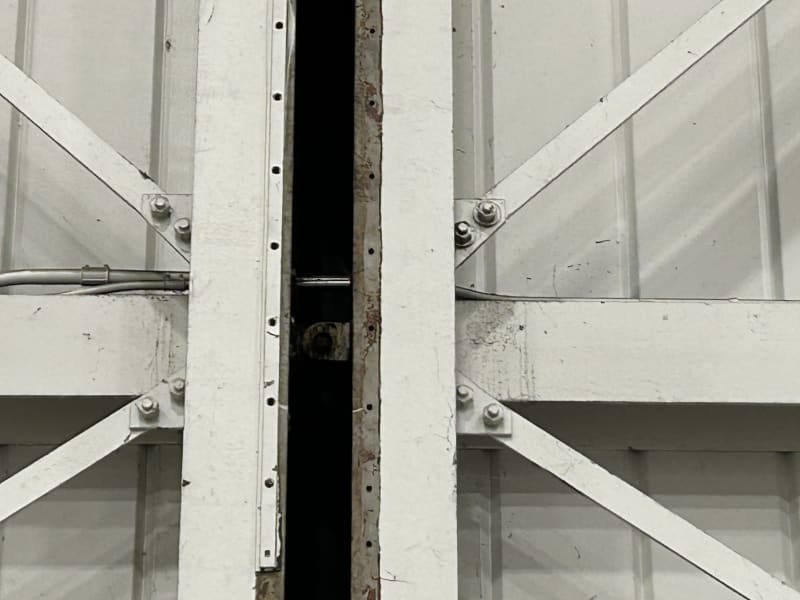
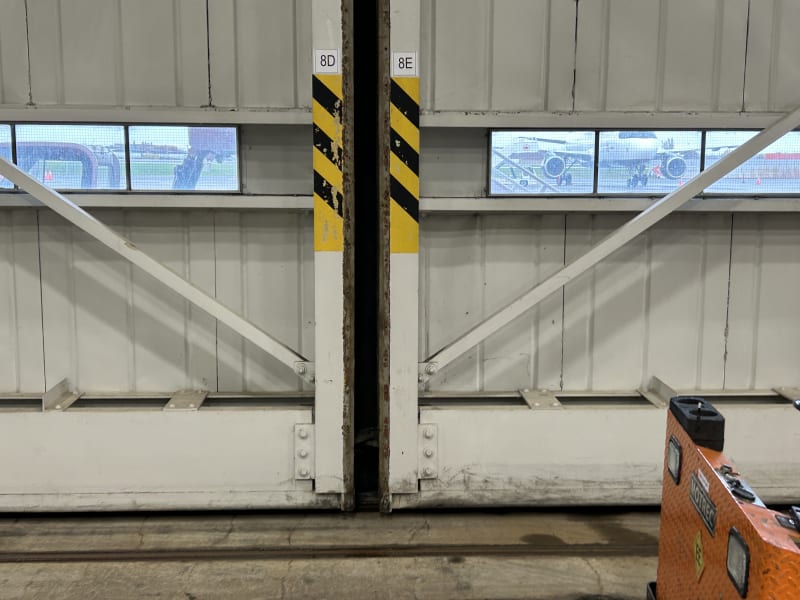
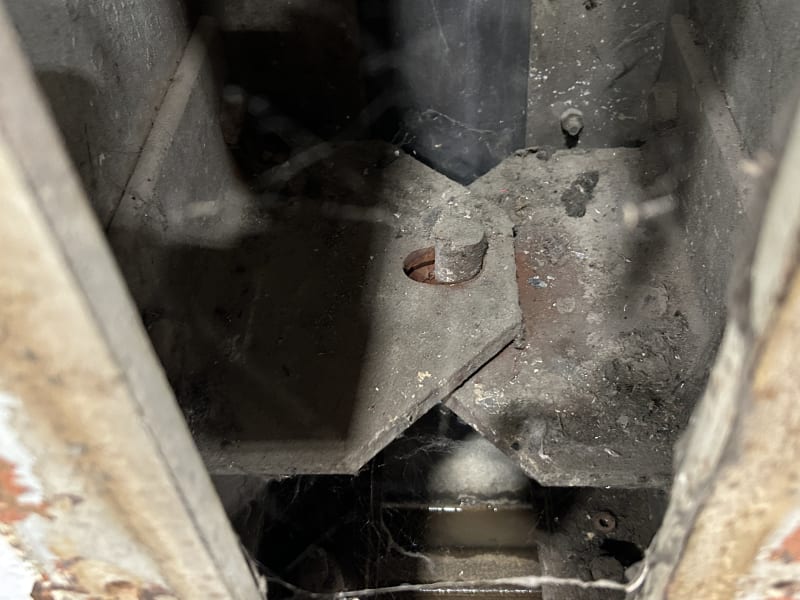
Initially, I thought these connections served to transfer transverse load from one panel to the other, and that the impact of force transfer was causing damage to the existing connections. However, my perspective changed after observing the door in operation. It appears that the load transfers through the top connection exclusively. The dowel of the bottom joint moves 1/2 inch parallel to the doors but does not transfer any load between the door panels (no contact between the two L sections).
The challenge I'm facing is understanding the purpose of these connections in order to design new ones. The damaged ones seem to have been installed in the years after the construction of the doors. The L sections on the "newer" connections lack slotted holes in the top angle, which may have caused the observed damage during maintenance when portions of the doors were lifted (refer to pictures for clarification).
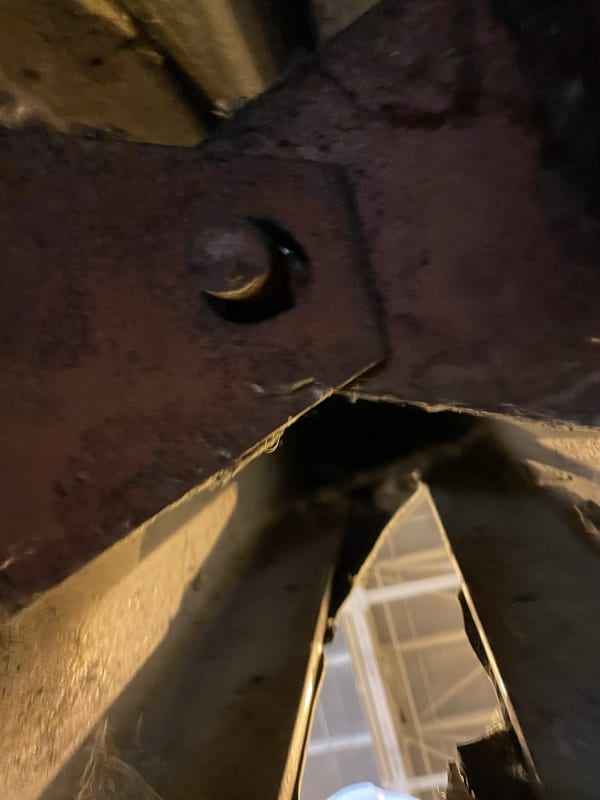
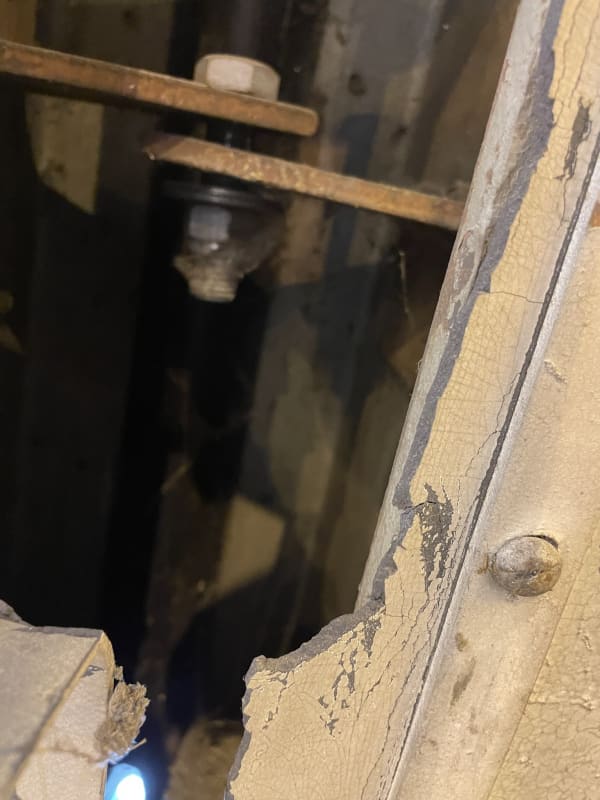
If anyone has experience in designing aircraft hangar doors and can provide insight into the purpose of these connections, it would be greatly appreciated.
Thank you.