Hi
Refer the image.
My requirements are:
1) 20 width slot shall be symmetrical to 50 length.
2) Depth of the 20 slot shall be within 0.2 symmetrical from dia 10 center line.
3) 5 width slot shall be perpendicular to datum C.
4) Depth of the 5 slot shall be within 0.2 symmetrical from dia 10 center line.
How to represent the GD&T for depth of slot wrt cylinder center line.
Shall I place profile of surface wrt datum A on flat face?
Thank you
Refer the image.
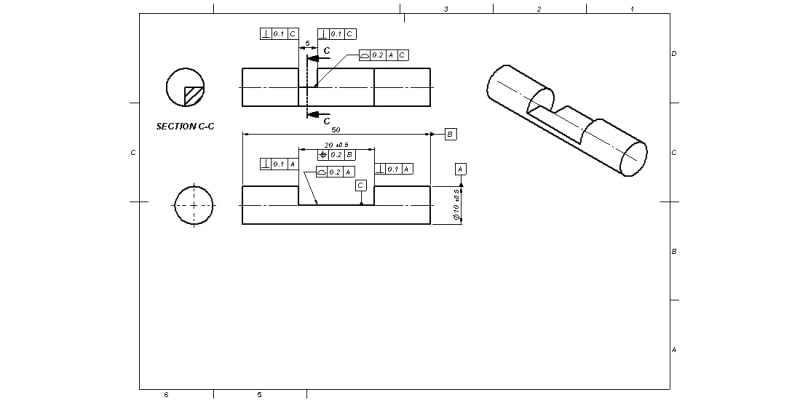
My requirements are:
1) 20 width slot shall be symmetrical to 50 length.
2) Depth of the 20 slot shall be within 0.2 symmetrical from dia 10 center line.
3) 5 width slot shall be perpendicular to datum C.
4) Depth of the 5 slot shall be within 0.2 symmetrical from dia 10 center line.
How to represent the GD&T for depth of slot wrt cylinder center line.
Shall I place profile of surface wrt datum A on flat face?
Thank you