KootK
Structural
- Oct 16, 2001
- 18,405
I'm doing a feasibility study on a small parking garage:
- 200' x 200'-ish.
- Two levels above grade.
- A rectangle if possible, a parallelogram if not.
- Coastal, high seismic (I'm not worried about this part).
- Precast TT and spandrel if the numbers make sense, mildly reinforced CIP if not.
My questions, which I'd like to have considered separately:
1) How viable is a parallel shaped parking structure like this in precast? I've had the good fortune to only EOR these things a sexy rectangles thus far. Can the ends be skew cut like I've shown? Got any better ideas for layout, especially at the top right? whatever I do will have to make sense for drainage.
2) How viable would a rectangular parking structure this small be in precast? In my home market, precast usually comes out on top for anything of any appreciable size. This one is pretty darn small however. At some point, I'd have to think that there would be so few precast pieces that the scales would tip in favor of CIP.
- 200' x 200'-ish.
- Two levels above grade.
- A rectangle if possible, a parallelogram if not.
- Coastal, high seismic (I'm not worried about this part).
- Precast TT and spandrel if the numbers make sense, mildly reinforced CIP if not.
My questions, which I'd like to have considered separately:
1) How viable is a parallel shaped parking structure like this in precast? I've had the good fortune to only EOR these things a sexy rectangles thus far. Can the ends be skew cut like I've shown? Got any better ideas for layout, especially at the top right? whatever I do will have to make sense for drainage.
2) How viable would a rectangular parking structure this small be in precast? In my home market, precast usually comes out on top for anything of any appreciable size. This one is pretty darn small however. At some point, I'd have to think that there would be so few precast pieces that the scales would tip in favor of CIP.
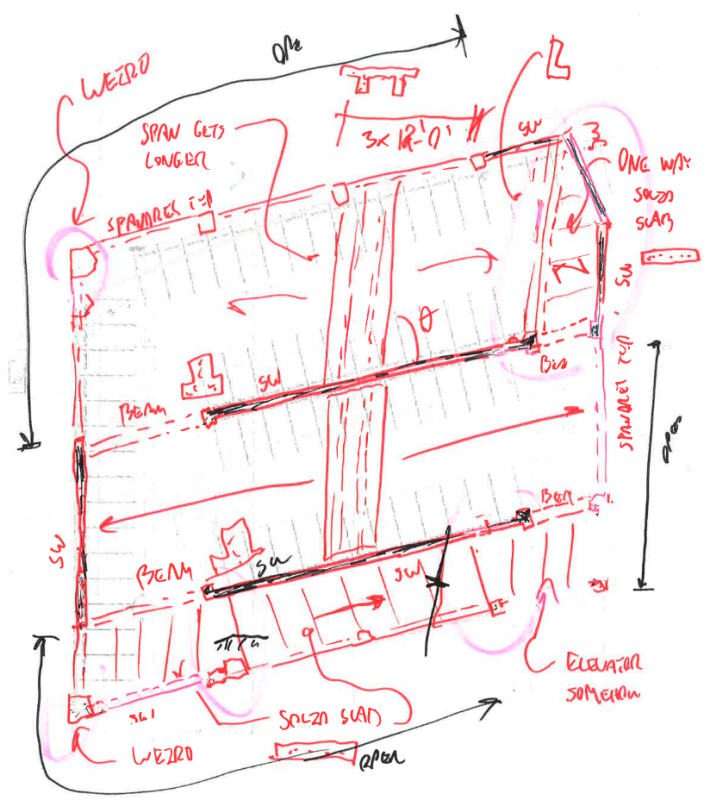