Dear colleagues,
I'm having a little problem here concerning contact between two solids.
I've modeled each part separately and then assembled them, I've defined and assigned boundary conditions, materials, meshes, constraints interactions, loads.
I've submitted the job, and everything seems to work except one interaction.
When I increase the scale factor for the deformed shape, one solid penetrates the other. I think this is not a graphical issue because when I plot CPRESS, it's non-zero in all the other contact places excepting this one.
Things I've tried:
General Contact - Without modifications. All the interactions worked except the troublesome one
General Contact - Plus Surface to surface contact in the problem region - Slave surface with finer mesh than Master. - Same result
General Contact excluding the three surface with the problem, and defining manually Surface to surface contact on them - Same result
Same as above, adding Automatic surface smoothing in the manually defined contact region - Same result.
I don't think defining every interaction manually would help here.
This is an image of the undeformed model
Here's the deformed shape
Another view. CPRESS is zero in the vertical Pipe.
The two collinear pipes are compressed, The difference in compression is 45tons. I think the vertical plate welded to the vertical pipe should press against the last one.
The "weld" is modeled geometrically and tied to the vertical pipe.
I'm out of ideas here.
Any help or comment would be very much appreciated
I'm having a little problem here concerning contact between two solids.
I've modeled each part separately and then assembled them, I've defined and assigned boundary conditions, materials, meshes, constraints interactions, loads.
I've submitted the job, and everything seems to work except one interaction.
When I increase the scale factor for the deformed shape, one solid penetrates the other. I think this is not a graphical issue because when I plot CPRESS, it's non-zero in all the other contact places excepting this one.
Things I've tried:
General Contact - Without modifications. All the interactions worked except the troublesome one
General Contact - Plus Surface to surface contact in the problem region - Slave surface with finer mesh than Master. - Same result
General Contact excluding the three surface with the problem, and defining manually Surface to surface contact on them - Same result
Same as above, adding Automatic surface smoothing in the manually defined contact region - Same result.
I don't think defining every interaction manually would help here.
This is an image of the undeformed model
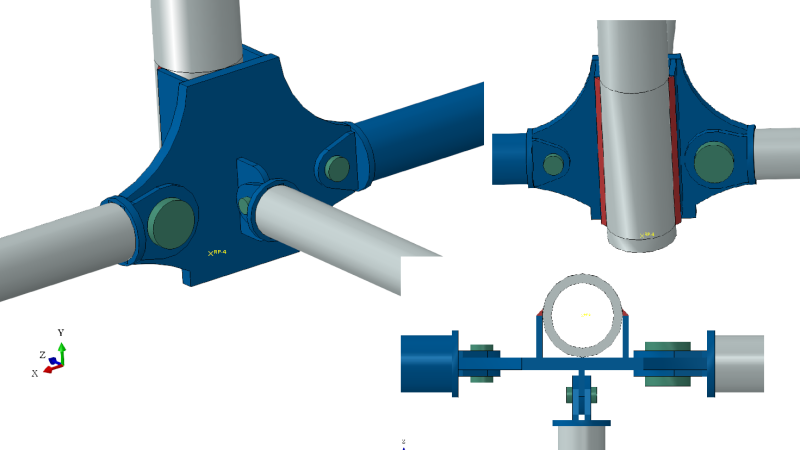
Here's the deformed shape
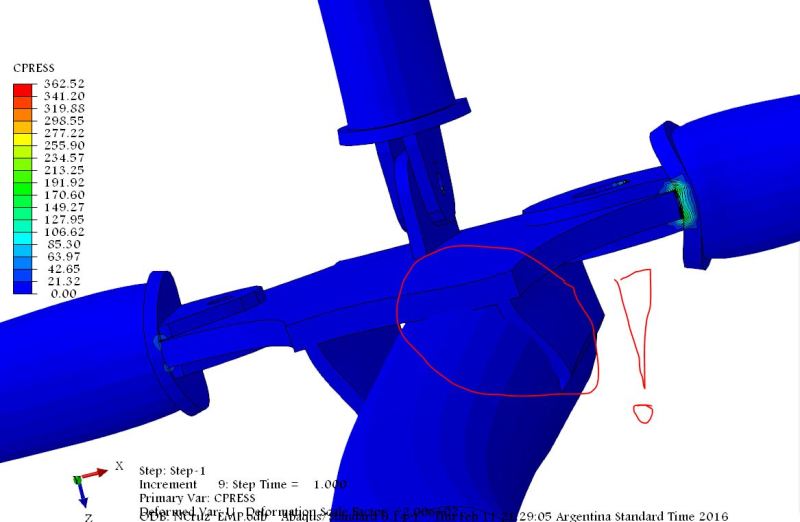
Another view. CPRESS is zero in the vertical Pipe.
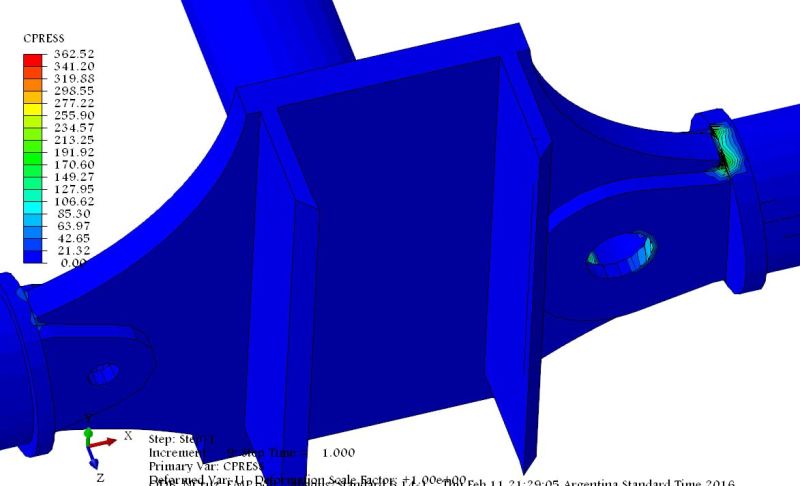
The two collinear pipes are compressed, The difference in compression is 45tons. I think the vertical plate welded to the vertical pipe should press against the last one.
The "weld" is modeled geometrically and tied to the vertical pipe.
I'm out of ideas here.
Any help or comment would be very much appreciated