Aytacoglu
Civil/Environmental
- Dec 4, 2023
- 40
Hi All,
I need to check a connection for a steel beam that will be cut at its end (300mm from the edge). New beam will be installed which will be back to back channel sections (180x75PFC). These are going to be spliced together at the web and bottom flange (top flange splice avoided due to site clashes).
I want to check the connection to ensure this will work. Can anyone please assist me on how to go with this? Is it the case that the main design check will be with the bolts connected at the web which needs to be checked against the shear plus the additional force exerted by the bending moment?
I attached the details below:
Thanks
I need to check a connection for a steel beam that will be cut at its end (300mm from the edge). New beam will be installed which will be back to back channel sections (180x75PFC). These are going to be spliced together at the web and bottom flange (top flange splice avoided due to site clashes).
I want to check the connection to ensure this will work. Can anyone please assist me on how to go with this? Is it the case that the main design check will be with the bolts connected at the web which needs to be checked against the shear plus the additional force exerted by the bending moment?
I attached the details below:
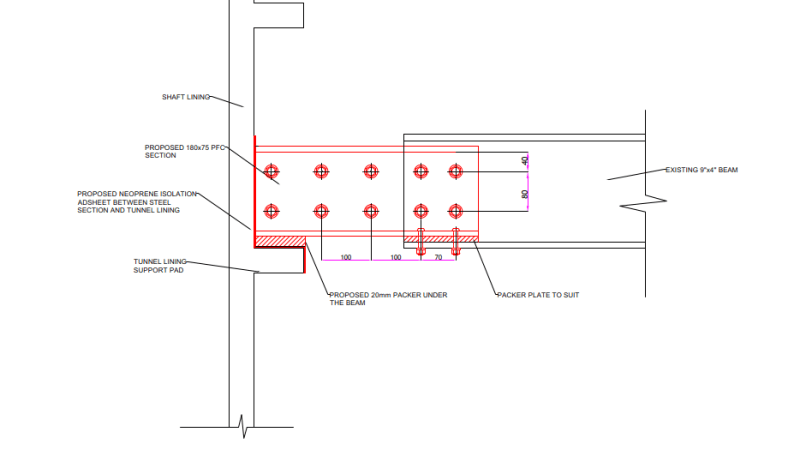
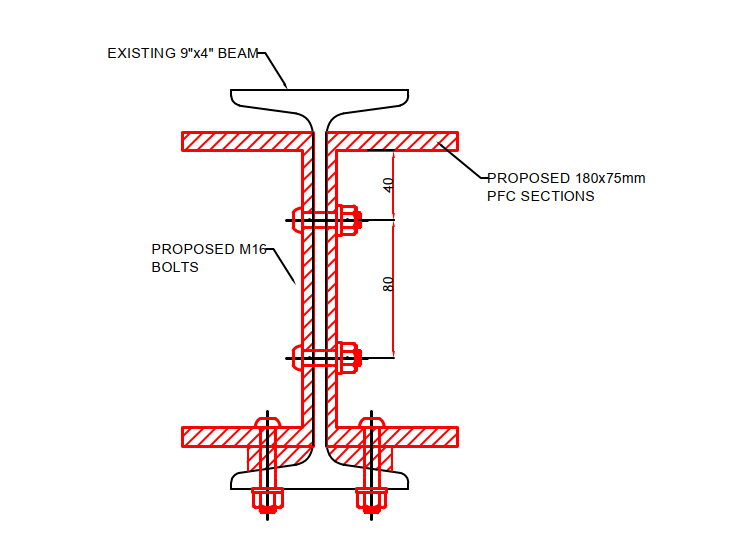
Thanks