Catee
Structural
- Jan 11, 2024
- 6
Dear All,
In general, we plan to perform a bolted splice connection for the large built-up section steel structure. I have a question regarding the possibility of executing a splice connection using the complete penetration joint (CPJ) welding method. The attached image illustrates a bolted splice connection. If the contractor wishes to change the connection type to a complete penetration joint (CPJ), is it feasible according to engineering principles? Moreover, does it ensure structural safety? The mentioned structure is a portal frame with concrete columns and large box-section steel beams as the crossbeam. This structure supports the guideway beam of a train monorail system.
In general, we plan to perform a bolted splice connection for the large built-up section steel structure. I have a question regarding the possibility of executing a splice connection using the complete penetration joint (CPJ) welding method. The attached image illustrates a bolted splice connection. If the contractor wishes to change the connection type to a complete penetration joint (CPJ), is it feasible according to engineering principles? Moreover, does it ensure structural safety? The mentioned structure is a portal frame with concrete columns and large box-section steel beams as the crossbeam. This structure supports the guideway beam of a train monorail system.
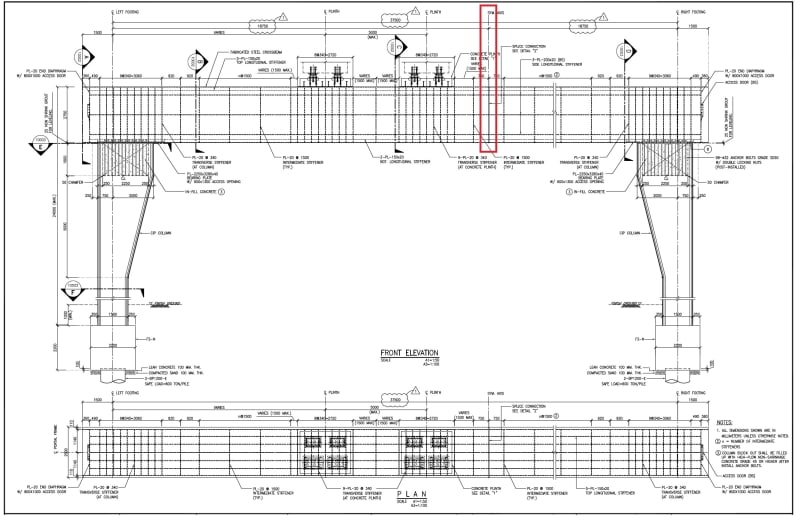
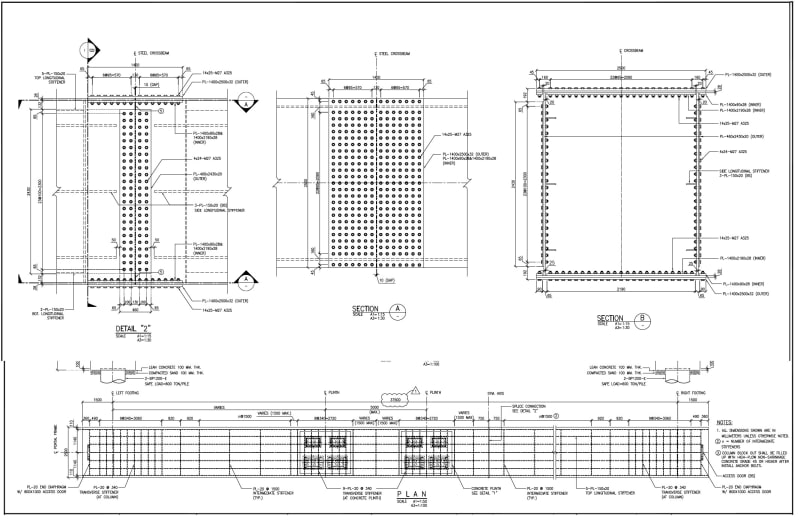