jerry1423
Mechanical
- Aug 19, 2005
- 3,428
The picture below shows a portion of a very large casting.
The holes in the top flange are drilled thru with the bottom end spot faced.
How does the machinist spot face the bottom of these holes ? Does he do it from the top with a special mill from the top ?
Jerry J.
UGV5-NX11
The holes in the top flange are drilled thru with the bottom end spot faced.
How does the machinist spot face the bottom of these holes ? Does he do it from the top with a special mill from the top ?
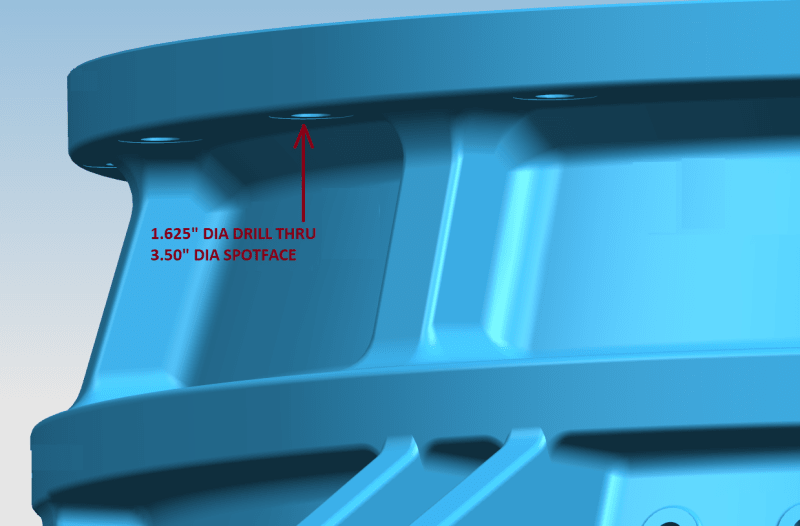
Jerry J.
UGV5-NX11