Rohitha Rathnaweera
Industrial
Good day Elites!
I'm having a challenge in updating the sprinkler fire protection system of a 50 year old cigarettes manufacturing and storage facility and have faced some challenges.
Dimensions of each storage - 20 x 22 meters, Roof height 7.5 meters and sprinklers mounted here.
Storage rack type - Drive in, continues racks with dimensions of -
L- 15 m, Depth - 12 m, triple row up to exact 5.9 m height to the top
Longitudinal flue space - 30 cm
Transverse flue space - 10 cm
Finished cigarettes boxes (corrugated cardboard) placed on "Fully closed boarded deck" wooden pellets which could delay the fire from going upwards. No any other mix of commodities.
My challenges -
Original system including piping and pneumatic tank were designed to cater for Grinnell 5.6K sprinklers (over 3800 heads). An insurance auditor visited recently has informed to change the system to deliver a density of 21.24 lmp/m2 using K8 sprinklers and upgrade pipe schedule and pumps which is not financially viable. (No explanation how this figure was reached).
In my understanding with NFA 13(2019),
Tobacco and finished products are Class III commodities (20.4.3.1).
Since the height to top of the boxes are 5.9 meters, can I use "Class III Density requirements up to 6.1 m" - 21.2.2.1 graphs with "Density vs storage height" 21.2.2.3 graph?
Current K5.6 sprinklers operating at 5 bar (at pump) delivering 150 l.p.m with a density of minimum 14.5 l.p.m. /m2 on ground and as per the 21.2.2.1 graphs, this should be sufficient.
If not sufficient by any mean, I propose to add "In-rack sprinklers" if it really needed.
Appreciate comments and advice. All comments and suggestions are welcome!
Thanks a lot in advance.
I'm having a challenge in updating the sprinkler fire protection system of a 50 year old cigarettes manufacturing and storage facility and have faced some challenges.
Dimensions of each storage - 20 x 22 meters, Roof height 7.5 meters and sprinklers mounted here.
Storage rack type - Drive in, continues racks with dimensions of -
L- 15 m, Depth - 12 m, triple row up to exact 5.9 m height to the top
Longitudinal flue space - 30 cm
Transverse flue space - 10 cm
Finished cigarettes boxes (corrugated cardboard) placed on "Fully closed boarded deck" wooden pellets which could delay the fire from going upwards. No any other mix of commodities.
My challenges -
Original system including piping and pneumatic tank were designed to cater for Grinnell 5.6K sprinklers (over 3800 heads). An insurance auditor visited recently has informed to change the system to deliver a density of 21.24 lmp/m2 using K8 sprinklers and upgrade pipe schedule and pumps which is not financially viable. (No explanation how this figure was reached).
In my understanding with NFA 13(2019),
Tobacco and finished products are Class III commodities (20.4.3.1).
Since the height to top of the boxes are 5.9 meters, can I use "Class III Density requirements up to 6.1 m" - 21.2.2.1 graphs with "Density vs storage height" 21.2.2.3 graph?
Current K5.6 sprinklers operating at 5 bar (at pump) delivering 150 l.p.m with a density of minimum 14.5 l.p.m. /m2 on ground and as per the 21.2.2.1 graphs, this should be sufficient.
If not sufficient by any mean, I propose to add "In-rack sprinklers" if it really needed.
Appreciate comments and advice. All comments and suggestions are welcome!
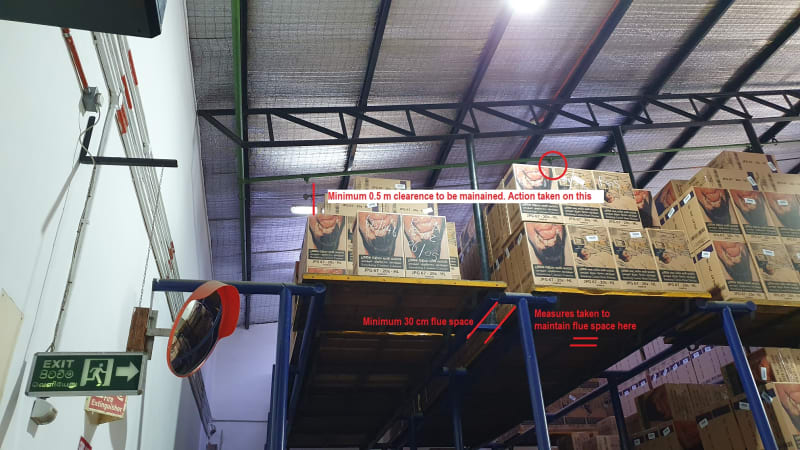
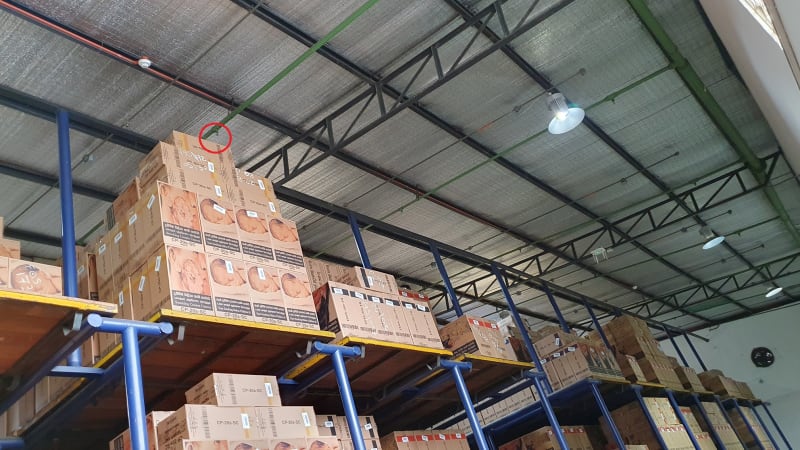
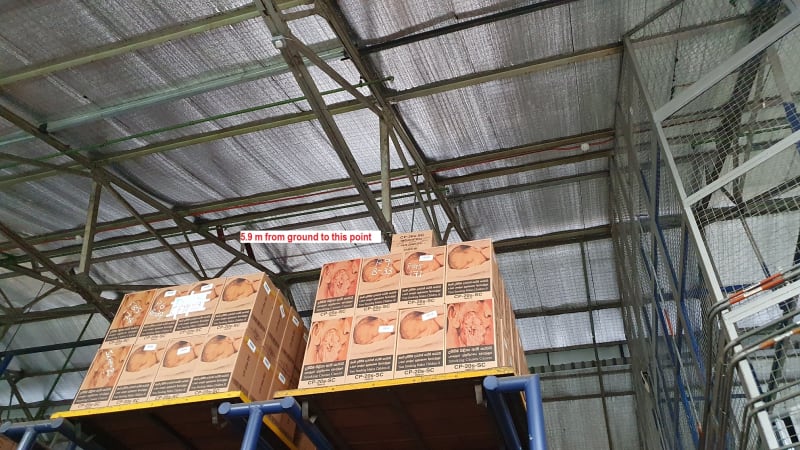
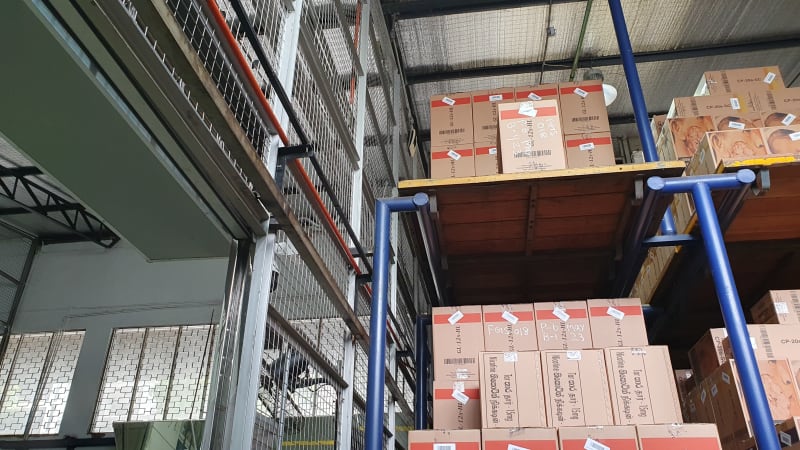
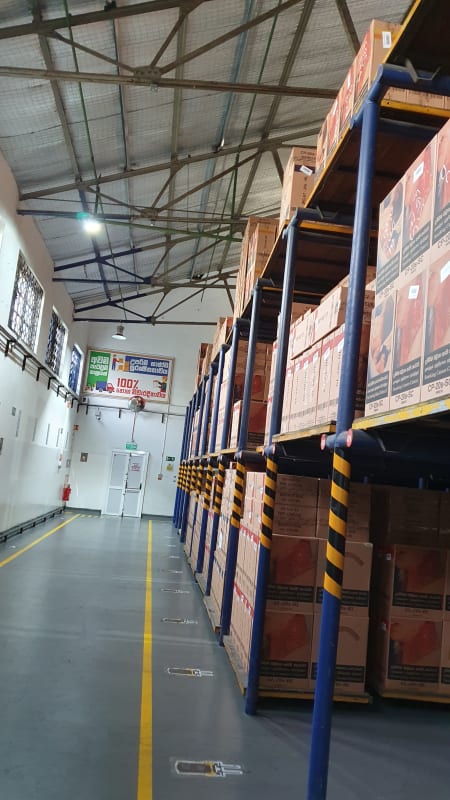
Thanks a lot in advance.