mats12
Geotechnical
- Dec 17, 2016
- 181
Im designing a steel canopy. All steel elements are hollow profiles (box profiles). All connetions are asummed as pinned. Because of that I braced a construction in roof plane
I have some thoughts about top of column - beam connection. I dont have much experiences with hollow/box profiles but in this case I have to use them.
Im wondering if connection shown in picture is alright in your opinion? Is there a better way?
Bolts are inside of a box profile so the beam would need to rotate quite a bit in order for considerable tension in bolts to develop. Is that right?
Bolts are definitely in tension when winds in blowing upward (resisting uplift) but forces are small.
Shear demands on bolts will be small too.
Is there anything Im missing? im not so confortable with shown connection (but it is aesthetically pleasing) so I want to make it sure before proceeding.
I have some thoughts about top of column - beam connection. I dont have much experiences with hollow/box profiles but in this case I have to use them.
Im wondering if connection shown in picture is alright in your opinion? Is there a better way?
Bolts are inside of a box profile so the beam would need to rotate quite a bit in order for considerable tension in bolts to develop. Is that right?
Bolts are definitely in tension when winds in blowing upward (resisting uplift) but forces are small.
Shear demands on bolts will be small too.
Is there anything Im missing? im not so confortable with shown connection (but it is aesthetically pleasing) so I want to make it sure before proceeding.
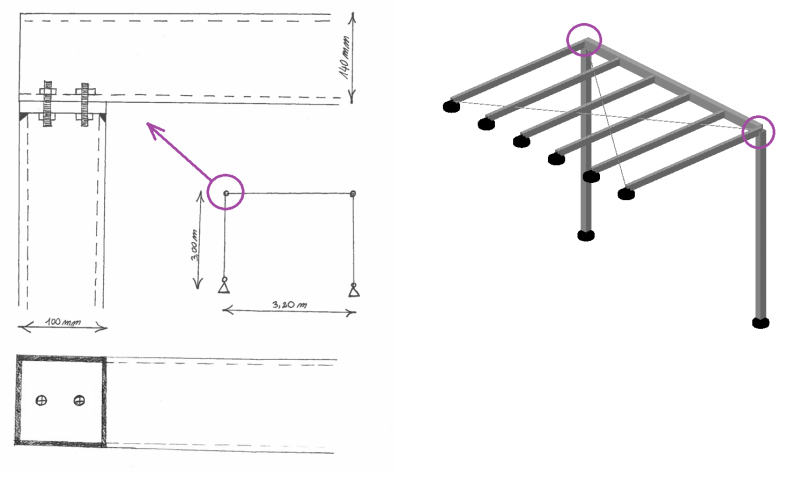
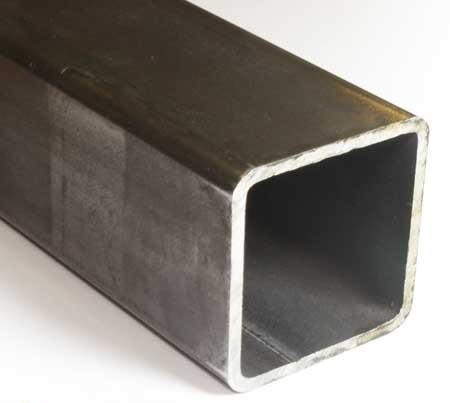