BZ29
Mechanical
- Jul 26, 2010
- 37
Received some pressure vessel drawings, having following data
ASME Sec VIII Div.2
Dia: 5500mm
Lenght: 20200mm
Thickness: 14(Shell) / 10(heads)
Hemispherical heads
supported on 3 saddles.
Vessel have internals of more than 20000kg
Although design is not in my scope of work, just curious to know, is there any guide or method to calculate these kind of partial stiffener rings (24 rings shown in drawing)?
I have checked myself, and without these partial stiffener rings, vessel design fails due to high circumferential stresses at tip of stiffener.
ASME Sec VIII Div.2
Dia: 5500mm
Lenght: 20200mm
Thickness: 14(Shell) / 10(heads)
Hemispherical heads
supported on 3 saddles.
Vessel have internals of more than 20000kg
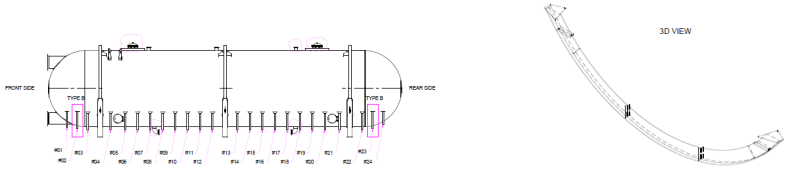
Although design is not in my scope of work, just curious to know, is there any guide or method to calculate these kind of partial stiffener rings (24 rings shown in drawing)?
I have checked myself, and without these partial stiffener rings, vessel design fails due to high circumferential stresses at tip of stiffener.