psychedomination
Structural
Hi there,
I'm working on a project where the client is trying to put a heavy piece of equipment on a roof. I ran a model and found that the beams the equipment will be resting on would be overstressed (~15%) and fail in bending (sagging only).
To strengthen the beam, I was looking to bolt a partial length cover plate to the bottom of the existing beam flange. I haven't done this type of strengthening before. In theory this seems quite simple, the additional section increases the section modulus, which then increases the moment capacity. However, when it comes to the detailing best practice, I can't find much guidance on this?
A few questions I have is :
1. What is the minimum spacing of bolts to take the shear flow. When I carried out the calculation, to take the shear flow the bolts only needed to be spaced 12" apart. However, I read online here : that the bolts should not be spaced more than the flange width apart. I went with this approach conservatively but I was wondering if this is general practice?
2. The cover plate is partial length (total length of beam is 25' but the cover plate only needs to be ~12' based on the applied moments). I have the end taper as 1' long (tapering from 6" to 2.5") with a fillet welded all around the tapered portion. Is there any guidance on sizing the end detail that someone can provide?
3. Am I missing anything here or is there anything I should be concerned about when considering construction? I oversized the width of the new plate slightly, allowing a 1/2" overhang on each end to allow the contractor to carry out a top down tack weld if they wanted to keep it in place when bolting. I'm not sure what other considerations I should include to ease construction?
Details I was thinking of using are below :
Any assistance/advice or guidance would be appreciated.
I'm working on a project where the client is trying to put a heavy piece of equipment on a roof. I ran a model and found that the beams the equipment will be resting on would be overstressed (~15%) and fail in bending (sagging only).
To strengthen the beam, I was looking to bolt a partial length cover plate to the bottom of the existing beam flange. I haven't done this type of strengthening before. In theory this seems quite simple, the additional section increases the section modulus, which then increases the moment capacity. However, when it comes to the detailing best practice, I can't find much guidance on this?
A few questions I have is :
1. What is the minimum spacing of bolts to take the shear flow. When I carried out the calculation, to take the shear flow the bolts only needed to be spaced 12" apart. However, I read online here : that the bolts should not be spaced more than the flange width apart. I went with this approach conservatively but I was wondering if this is general practice?
2. The cover plate is partial length (total length of beam is 25' but the cover plate only needs to be ~12' based on the applied moments). I have the end taper as 1' long (tapering from 6" to 2.5") with a fillet welded all around the tapered portion. Is there any guidance on sizing the end detail that someone can provide?
3. Am I missing anything here or is there anything I should be concerned about when considering construction? I oversized the width of the new plate slightly, allowing a 1/2" overhang on each end to allow the contractor to carry out a top down tack weld if they wanted to keep it in place when bolting. I'm not sure what other considerations I should include to ease construction?
Details I was thinking of using are below :
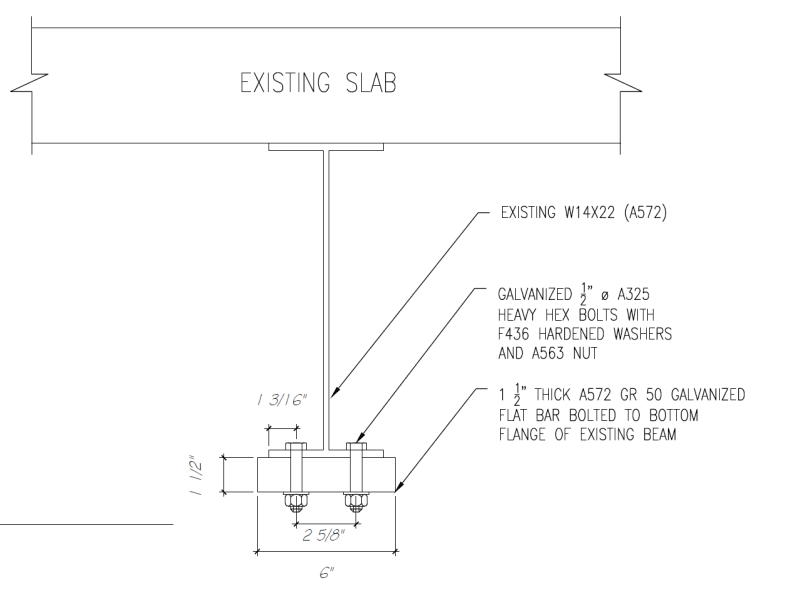
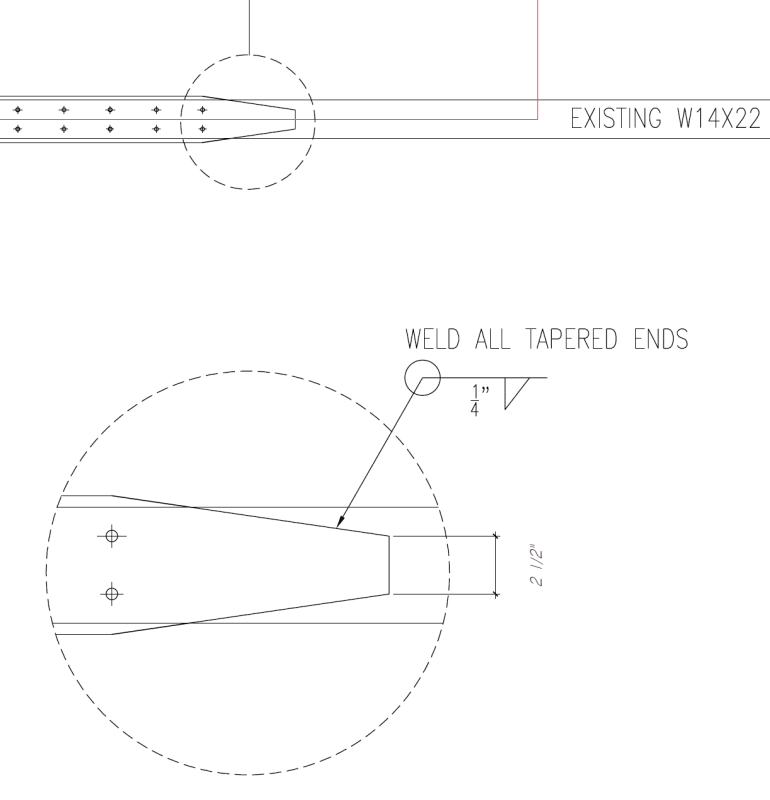
Any assistance/advice or guidance would be appreciated.