I am controlling the capacity of some existing beams in a structure for new loads. The beams are welded I sections, ~13m long, simply supported and it looks as if they will need reinforcing.
Some restrictions, limitations and other info
New columns cannot be added to reduce the span length.
They are under load and the load cannot easily be reduced as there is activity.
Temporary offloading by jacking up the beams is possible but not easy as the beam/slab is the third story.
They are only accessible from below, so only the bottom flange, the web and the underside of the top flange.
(Some of) The beams are already deflecting about 50mm, which limits the strengthening procedures, for example a "perfectly straight" section cant be inserted into or attached to the curved beam I assume.
The strengthening cannot add too much depth below the bottom flange.
The beams are quite tall and slender, 600-800mm tall with flanges about 350mm with a thin web.
The beams are primary beams, secondary beams are connected to them and brace them laterally at a few points reducing their buckling lengths.
Located in the EU if it makes a difference
I have searched and found some relevant threads but have a few questions.
Strengthening methods:
1. Welding of cover plates, I was thinking about adding a plate below the bottom flange, the plate being wider than the flange to get good (easier) welding from above. The plate could also be fitted in accordance with the curvature.
Thanks in advance and hope my English is sufficient to convey the questions.
Any input into the matter is appreciated.
Some restrictions, limitations and other info
New columns cannot be added to reduce the span length.
They are under load and the load cannot easily be reduced as there is activity.
Temporary offloading by jacking up the beams is possible but not easy as the beam/slab is the third story.
They are only accessible from below, so only the bottom flange, the web and the underside of the top flange.
(Some of) The beams are already deflecting about 50mm, which limits the strengthening procedures, for example a "perfectly straight" section cant be inserted into or attached to the curved beam I assume.
The strengthening cannot add too much depth below the bottom flange.
The beams are quite tall and slender, 600-800mm tall with flanges about 350mm with a thin web.
The beams are primary beams, secondary beams are connected to them and brace them laterally at a few points reducing their buckling lengths.
Located in the EU if it makes a difference
I have searched and found some relevant threads but have a few questions.
Strengthening methods:
1. Welding of cover plates, I was thinking about adding a plate below the bottom flange, the plate being wider than the flange to get good (easier) welding from above. The plate could also be fitted in accordance with the curvature.
Since it is under load, any welding will cause the section to soften due to the heat which I assume adds deflection. How much of an issue is this?
Since it is under load the bottom flange is already under tension stresses, while the new material should have (close to) no stresses, will this discrepancy cause issues?
If the cover plate is welded without (partially) unloading the beam, then the added material will only effect additional loads?
2. FRP reinforcement.While I (personally) cannot do this, I could recommend it to the customer if it is feasible, is this a viable solution to recommend? It adds no heat, is lighter/easier to handle than additional (heavy) steel profiles, seems less of a project than welding aswell
3. Post tensioning of the steel beamI have (briefly) read some texts about this and it seems good. If done properly it seems to me that i could even remove some of the deformations on the beam. For instance adding a kingpost type of solution
How is the connection properly done to the beam? Welding something to the thin web seems hazardous
Regarding the detailing, the image below shows three examples.
The first one should be easiest to do since it would only attach to the bottom flange. But since the bottom flange is bent downwards wouldn't the prestressing cause it to bend further down? (I know it is below the NA so it gives a negative moment that should cause the beam to bend upwards, but part of my brain worries I am missing something...
The second is the option I prefer, aside from the web connection at the ends ofc. The stiffeners where the tendon changes direction takes a compressive force upwards from the node causing the beam to elevate.
Welding will be required here but will be more localized at the "nodes" so that is an positive at least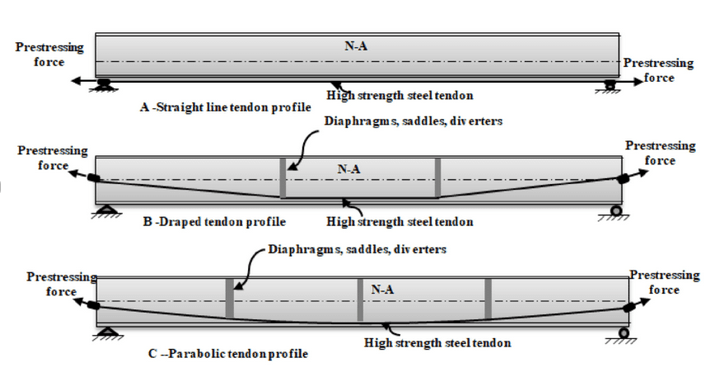
Thanks in advance and hope my English is sufficient to convey the questions.
Any input into the matter is appreciated.