sheafromme
Mechanical
- May 1, 2020
- 26
Hello,
I'm having trouble determining how to account for stress concentrations at the root of the flat on a motor shaft due to overhung radial loading. I inherited a motor/pulley assembly that has an propensity for the shaft to snap off right at where it transitions from a D-shape to circular cross section. The pulley pictured below has a belt on it that applies the loading.
There is not a fillet where the shaft changes profile
I've looked through most of the resources I have here and I can't seem to find anything that addresses this particular situation. It' probably because it's not a great design...
So, I was just wondering how to properly calculate the fatigue life or at least how to account for the huge stress concentrations at that transition point due to bending.
Thank you!
-Shea
I'm having trouble determining how to account for stress concentrations at the root of the flat on a motor shaft due to overhung radial loading. I inherited a motor/pulley assembly that has an propensity for the shaft to snap off right at where it transitions from a D-shape to circular cross section. The pulley pictured below has a belt on it that applies the loading.
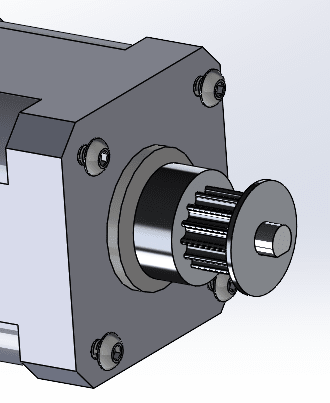
There is not a fillet where the shaft changes profile
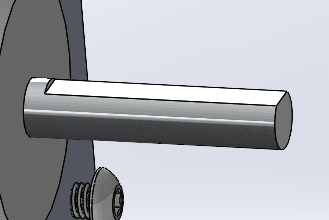
I've looked through most of the resources I have here and I can't seem to find anything that addresses this particular situation. It' probably because it's not a great design...
So, I was just wondering how to properly calculate the fatigue life or at least how to account for the huge stress concentrations at that transition point due to bending.
Thank you!
-Shea