Mr_Curious
Mechanical
- Jul 14, 2020
- 47
Hello Dear Experts.
I have a construction with lifting lugs. FEA analysis showed an area with the stress in lifting lugs higher than yield strength. The area is shown in the picture below (red color). The lugs were tested in real-life successfully. But I need to write a conclusion for my FEA analysis describing why this red zone does not dangerous. (real-life testing is not enough).
Help me please, what knowledge or books can I refer to?
I have a construction with lifting lugs. FEA analysis showed an area with the stress in lifting lugs higher than yield strength. The area is shown in the picture below (red color). The lugs were tested in real-life successfully. But I need to write a conclusion for my FEA analysis describing why this red zone does not dangerous. (real-life testing is not enough).
Help me please, what knowledge or books can I refer to?
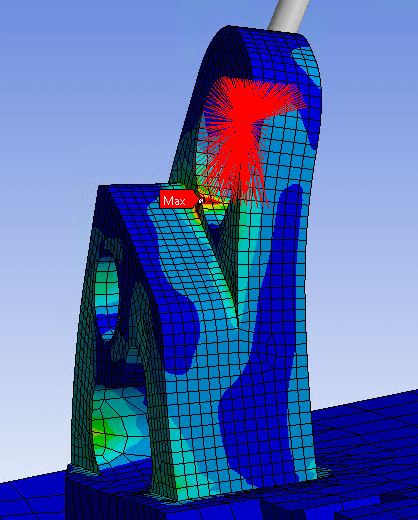
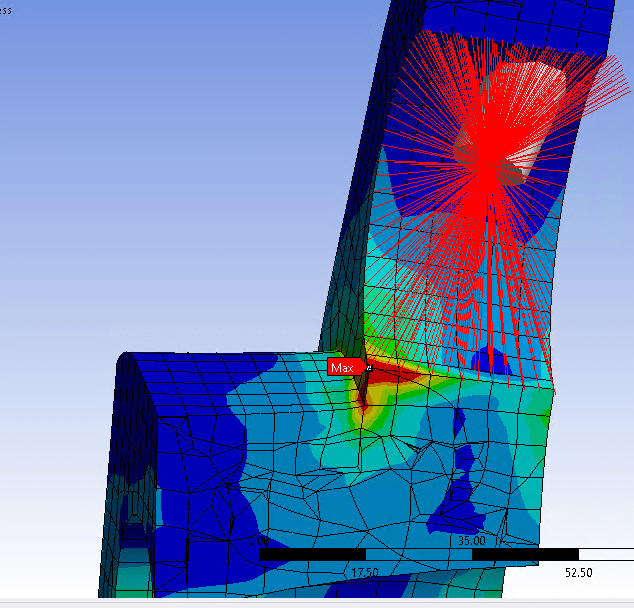